Yes. Proper storage of EV batteries is crucial. Be sure to label them appropriately and store them in a designated area like a storage building outside your facility or have (50) feet of separation between a stored battery and a building or another vehicle. The facility should be
temperature controlled and have a ventilation system.
Frequently Asked Questions
General Inquiries
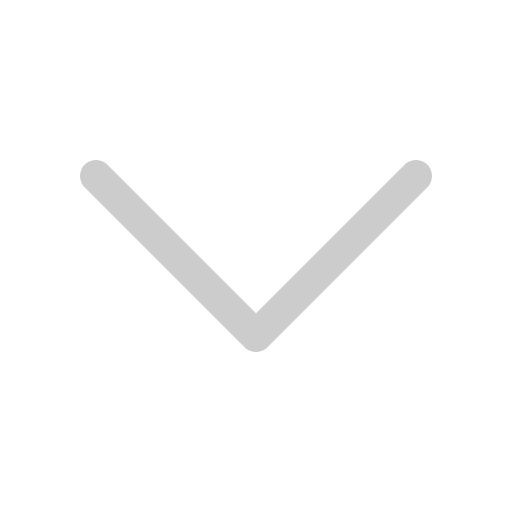
Should removed batteries require special storage?
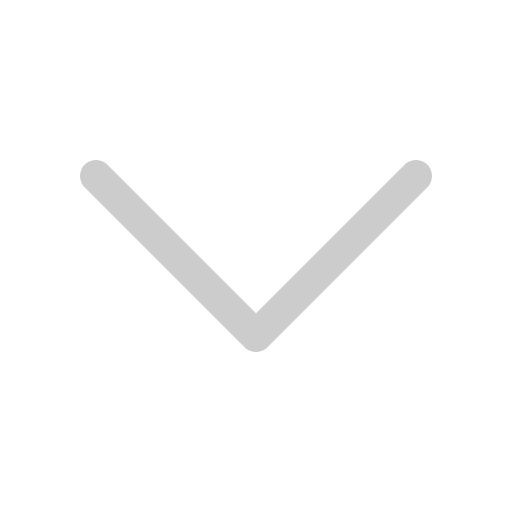
Do high voltage electric and hybrid vehicles pose significant danger during a repair?
Yes. Stronger batteries in EVs are high-voltage energy systems and can be dangerous and even deadly if not handled correctly. Always use extra care and consideration when working with these systems. Every aspect of the EV runs on electricity and potentially hold a dangerous charge even with the vehicle turned off.
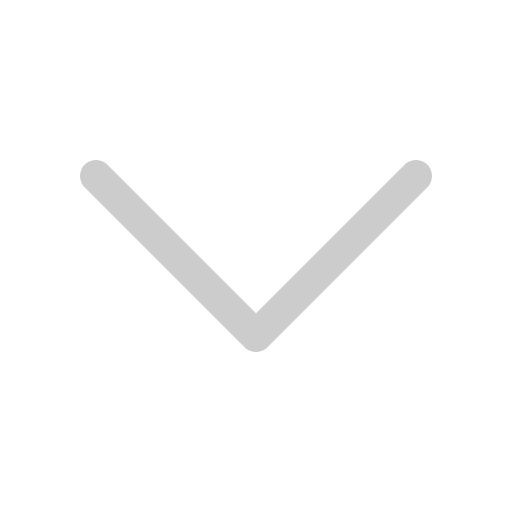
Will there be future advancements/improvements in technology, charging infrastructure,and services capabilities?
Yes. Electric vehicle and battery technology is evolving at a rapid pace. Groundbreaking research and technological improvements are greatly reducing battery prices, improving driving range and reducing the overall price for EVs.
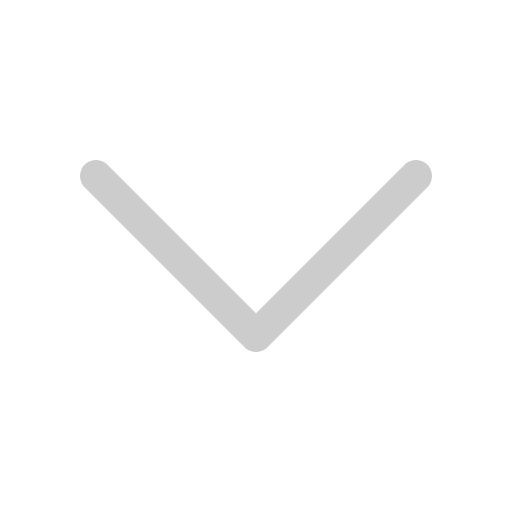
Do I need a designated area for repairs?
Yes. You must commit a designated space within your shop for EVs and access must be limited to those authorized to work in the space. Barricades and other off-limits designations are important elements to reinforce the importance of this dedicated space.
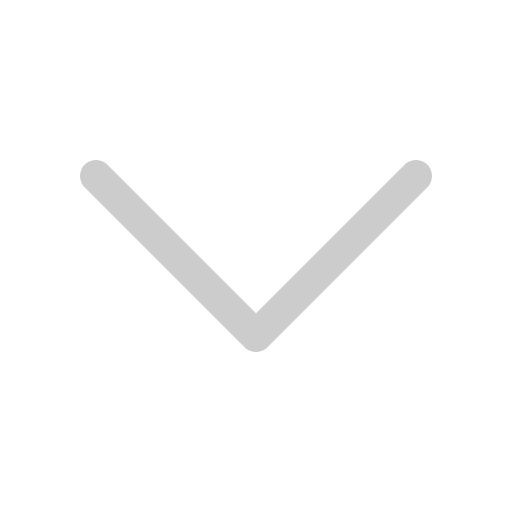
Are EV repairs a good choice for shop owners?
Yes. As EV sales continue to increase, the demand for repair and maintenance services will inevitably increase. Repair shop owners can diversify their services and invest in EV training and equipment, positioning them as leaders in the expanding EV repair market.
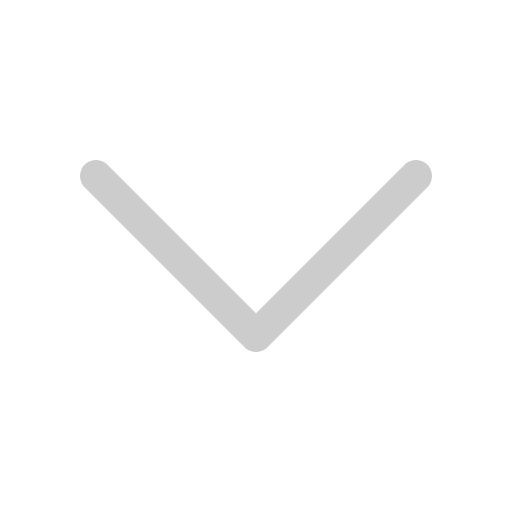
Do I need an EV service area barricade kit?
Yes. You will need a service area barricade kit to prevent or limit access to work areas with live electrical components and repairs. JDI’s Service Area Barricade Kit includes (6) red and white posts, (1) 82-foot plastic chain, and (2) plastic warning signs.
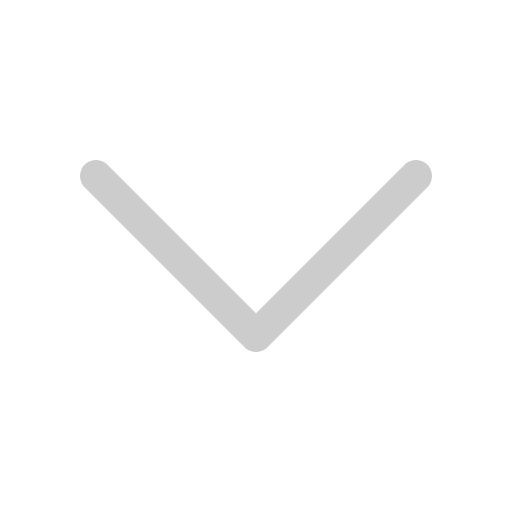
Should technicians always follow OEM guidelines and manuals?
Yes. It is critical to utilize OE service information and procedures for every EV or Hybrid. While there are standard service procedures, exact procedures of different vehicle makes will vary, and technicians need to follow these by the letter. OEM Manuals provide precise model-specific information straight from the manufacturer. Opting to use OEM guidelines and manuals ensures accuracy, reliability, reducing the risk of incorrect repairs or further damage to the vehicle.
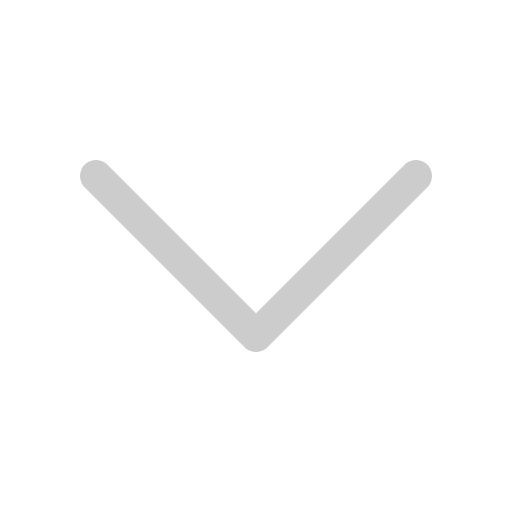
Do technicians need a certificate in EV repair?
EV training requires certification, showing a technician’s expertise and competence. It indicates completion of a rigorous program and the ability to service EVs safely and effectively.
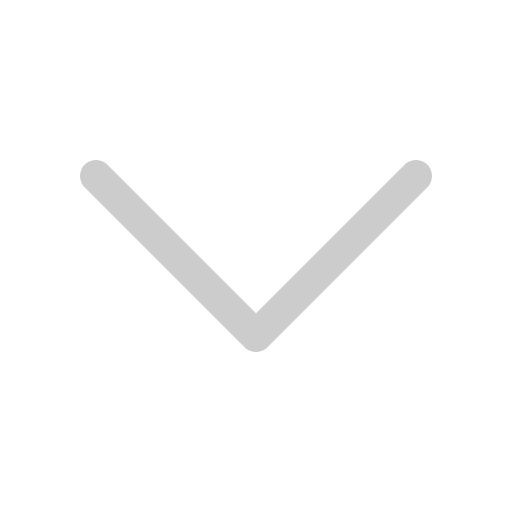
Do technicians need special EV repair training?
Yes. The investment in training by the shop owner and the technician is a necessary investment in the future. EV-focused repair courses prepare technicians on how to safely repair these vehicles. The Institute of the Motor Industry (IMI) has been increasing its EV Skills
Training offerings regularly. ASE has launched its EV Safety Testing & Certification Program. In addition, several EV manufacturers offer specialized training programs for their own EVs.
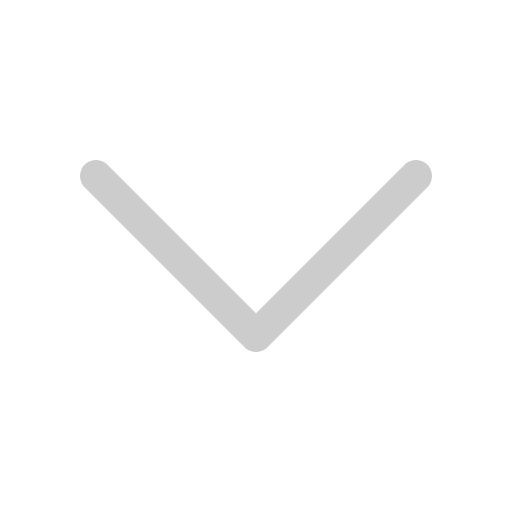
What is Thermal Runaway?
Thermal runaway is one of the primary risks related to lithium-ion batteries. It occurs in an EV when its battery’s internal reactions cause a self-reinforcing cycle of increased heat production. This means the battery continues to get hotter by itself until the battery reaches its
limits or experiences a catastrophic failure like a fire.
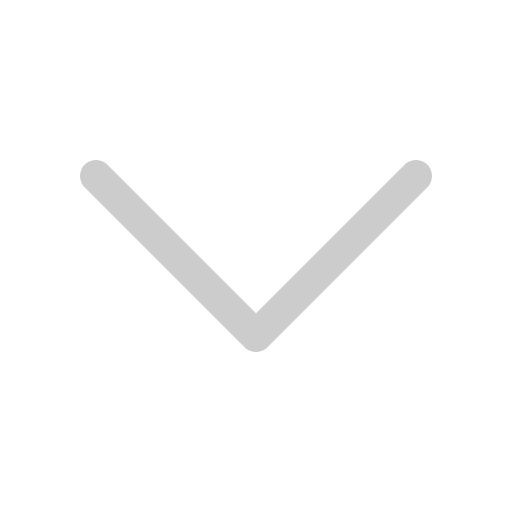
Why do I need a vehicle fire blanket?
EV lithium-ion battery fires are very difficult to extinguish and traditional fire repellents do not work. An EV battery’s internal reactions can cause a self-reinforcing cycle of increased heat
production meaning the battery continues to get hotter by itself until the battery reaches its limits or experiences a catastrophic failure like a fire (a process known as thermal runaway). The Vehicle Fire Blanket is the most efficient way to isolate an EV fire. It immediately isolates the fire/fumes and prevents spreading. While it will slowly smother/contain the fire, it will not put out the EV fire. It will control the fire until the Fire Department arrives.
A Vehicle Fire Blanket enables you to suppress EV, Hybrid, and ICE vehicle fires, flames and fumes. While preventing the fire from spreading and damaging vehicles and shop property.
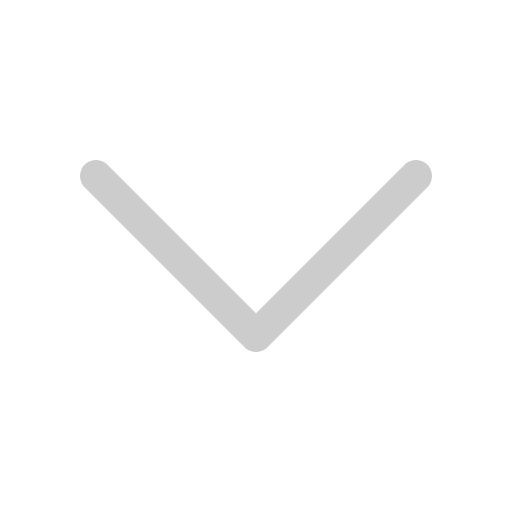
What does lock out/tag out mean?
Lock Out/Tag Out (LOTO) is a safety procedure ensuring an EV is properly disconnected to complete repair work. Appropriate car signage is required and a Locking Steering Wheel Cover
prevent technicians from accidental vehicle re-energizing. The Cover includes a strap closure at the back with metal eyelets designed for a Nylon Safety Padlock securing the Cover to the steering wheel. This device is an integral part of a LOTO procedure designed to meet the OSHA standard for the Control of Hazardous Energy.
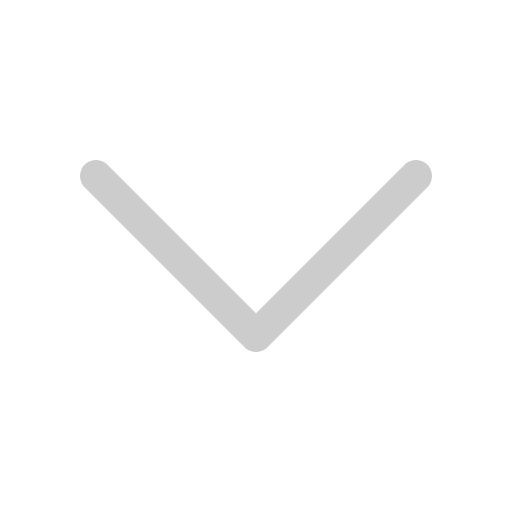
Can I repair an EV in one of my existing bays?
Yes. However your bay must include specific items different than a standard bay. While renovations are always an option, if you are working with an existing space, you must commit a designated area for BEV/HEV repairs ONLY with clear indication of limited access to those authorized to work within the space.
Here are a few things you need to include in your EV/Hybrid bay:
– Yellow and black tape and caution/danger signage
– Service area barricade equipment including high voltage warnings
– A Shepard’s rescue hook
– Lock out/Tag out procedures and signage
– PPE for your technicians
– Insulated repair tools
Be mindful of the capital investment you will need to make when repairing EVs and Hybrids. These investments can include EV lifts, EV battery lifts, charging stations, electric test tools, equipment for programming onboard software and EV-compatible diagnostic equipment.
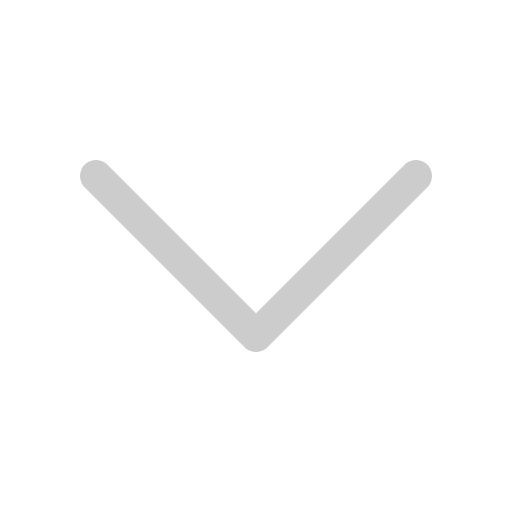
What type of safety equipment do I need for my repair shop?
In the world of EV repair, having the right safety equipment is non-negotiable. You must equip your shop with PPE items including (but not limited to) EV gloves, specialized clothing, appropriate footwear, rubber mats, a shepherd’s rescue hook, a fire blanket in case of a fire,
and a device for verifying the vehicle’s safe for repairs. For a full catalog of EV safety equipment, click here.
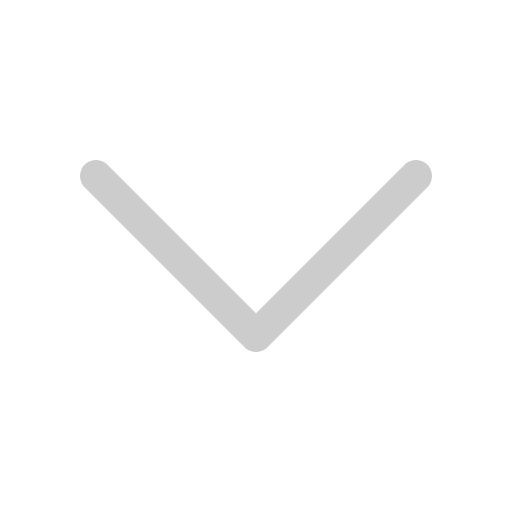
What kind of EV repair tools do I need to look for?
Using certified insulated tools is essential in preventing the high risk of electrocution. The most needed tools are pliers, ratchets, screwdrivers, sockets, spanners, multimeters, high voltage probes, and insulated resistance testers. Equipment needs include EV lifts, EV battery lifts, charging stations, electric test tools, equipment for reprogramming onboard software, and EV-compatible diagnostic equipment.
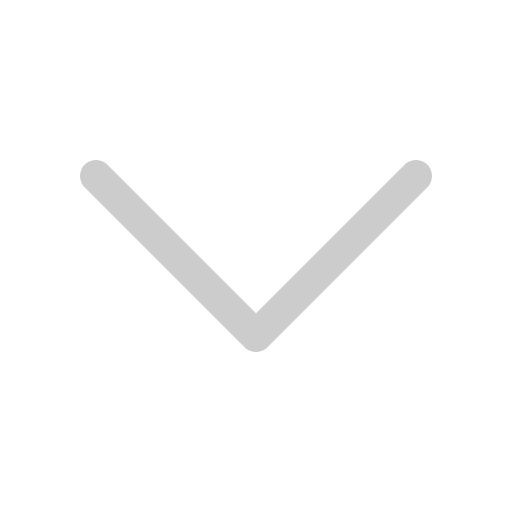
What is PPE and why do I need it?
Personal Protection Equipment (PPE) refers to clothing, equipment or tools designed to protect individuals from potential hazards while servicing an EV, significantly reducing the risk of accidents, injuries, and exposure to electrical issues.
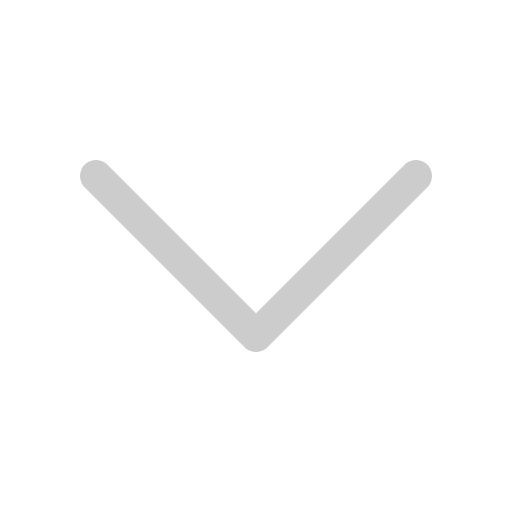
What are the most common EV repairs?
EV batteries, tires, brakes, coolant replacement, fluid checks, wiper blades, and cabin air filters
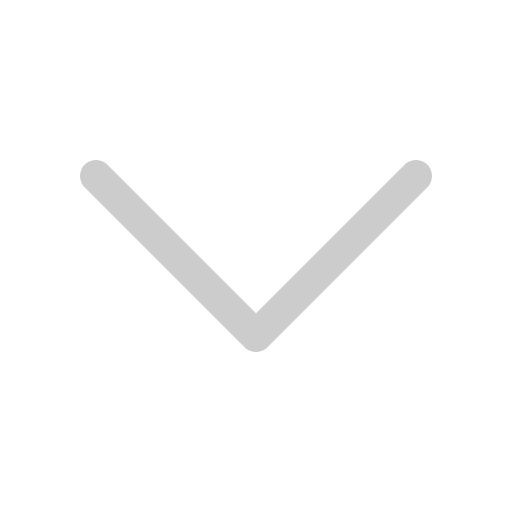
Do I need to test my gloves?
Yes, however it varies by class. For example Class 0 gloves, a common glove used with repairing EVs, must be tested by a blow test (either by manually blowing into the glove to identify any holes or leaks, or by using a Pneumatic Glove Tester. They should be tested before each use with a blow test and every (6) months thereafter and upon indications the insulating value is suspect. The OSHA Regulation 29 CFR 1910.137 states all insulating equipment must be inspected for any damage before each day’s use and immediately following any incident that can reasonably be suspected.
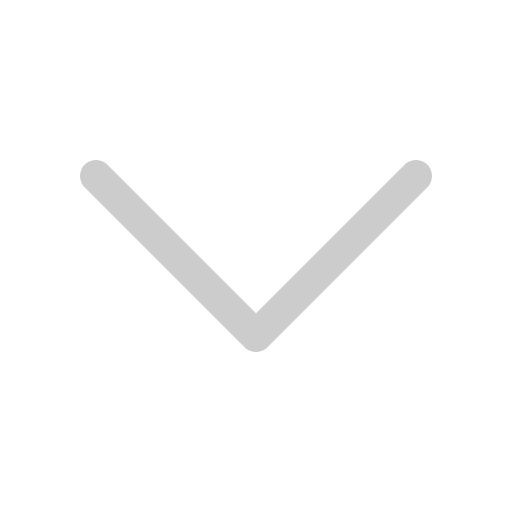
Does EV repair equipment need to be certified?
Yes. Any repair product used with electric vehicles must comply with OSHA and IEC standards.
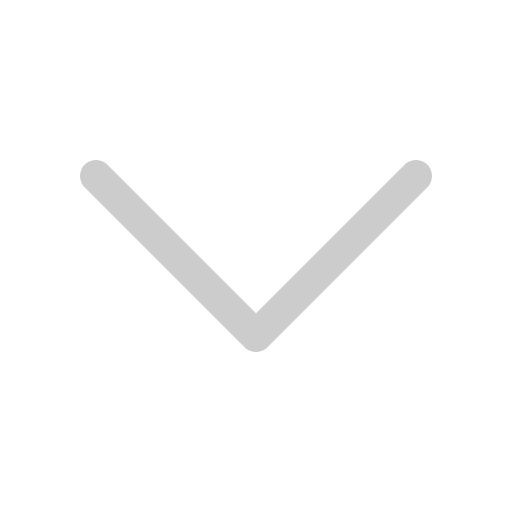
Do I need to only get rubber gloves?
No. You must follow all OSHA safety regulations regarding working on electric vehicles, which requires qualified technicians working on or near energized electric vehicles wear insulating rubber gloves (with the correct class for the voltage) with leather protector gloves.
We recommend also wearing cotton under gloves for better comfort. Layer your gloves in this order: Hand>Cotton Under Gloves>Insulating Rubber Gloves>Leather Over Gloves.
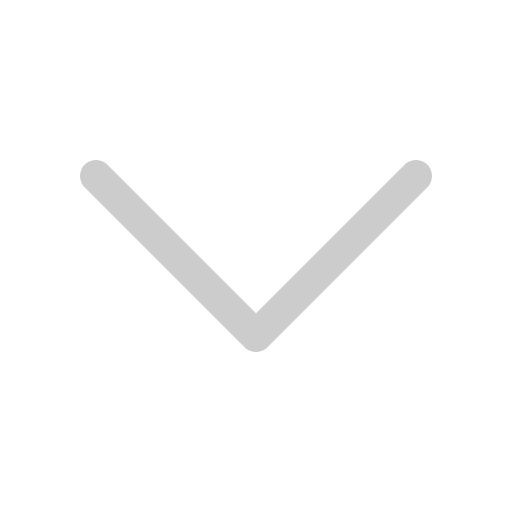
What size EV repair gloves do I need?
First you need to determine what voltage you are working with. All EV repair gloves are rated – and color coded – by the maximum voltage the gloves can withstand. It is generally accepted by EV manufacturers Class 0 gloves are the proper choice when working on EVs, as they are rated at 1,500 volts DC maximum use voltage. You must identify what class gloves you need before ever working on a potentially charged electric or hybrid vehicle.
Insulated rubber gloves are not one-size-fits-all. Purchase gloves based on the hand size of the technician using them. Some glove manufacturers only offer small, medium, and large. Others offer half sizes, in inches.
Always choose the same size gloves. For example, if you wear size 10 insulating Rubber Gloves, choose size 10 in the over and under gloves. For complete comfort and safety, the three types of gloves are to be layered as follows: cotton under gloves/insulating rubber gloves/leather over gloves.
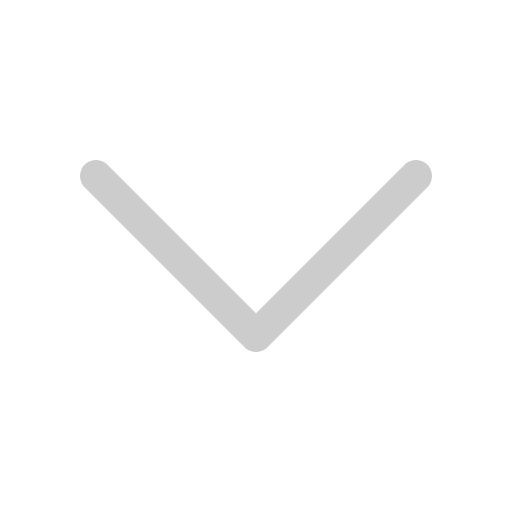
What are EV repair gloves and why do I need them?
EV repair gloves are personal protective equipment (PPE) that protects you from electrical shock when working near live voltage on an EV. Electric and hybrid vehicles are not like internal combustion vehicles, where they can put off a significant amount of voltage. Repairers need to protect themselves from these potentially deadly electric shocks when repairing an EV or Hybrid.
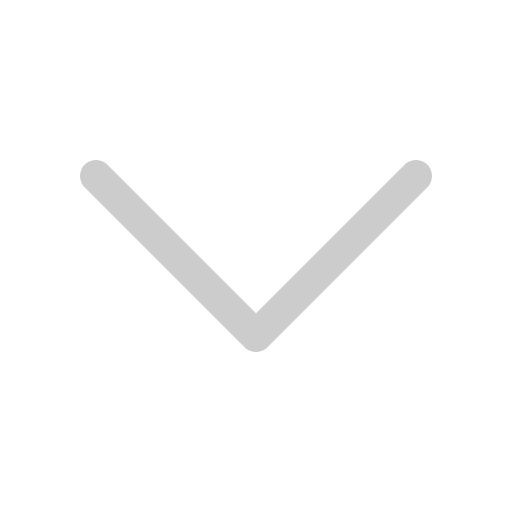
Do you have an application guide?
We have a TPMS Application Guide to provide technicians with Year-Make-Model (Y-M-M) lookup information.
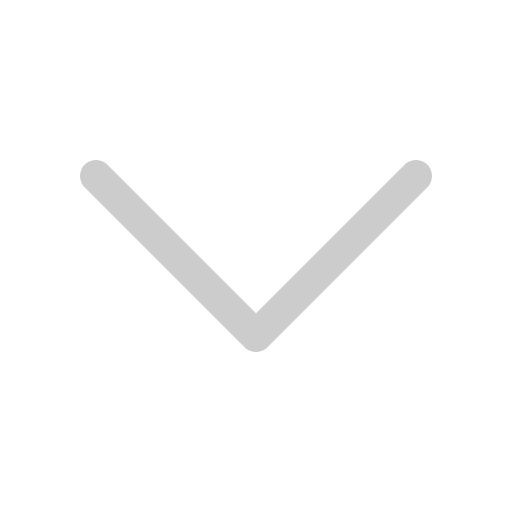
How can I find a part for a specific vehicle?
You can find or Wheel Nut/Studs, Drain Plugs/Gaskets and TPMS application parts by Year, Make, Model using our Application Search on our Johndow.com/tpms website.
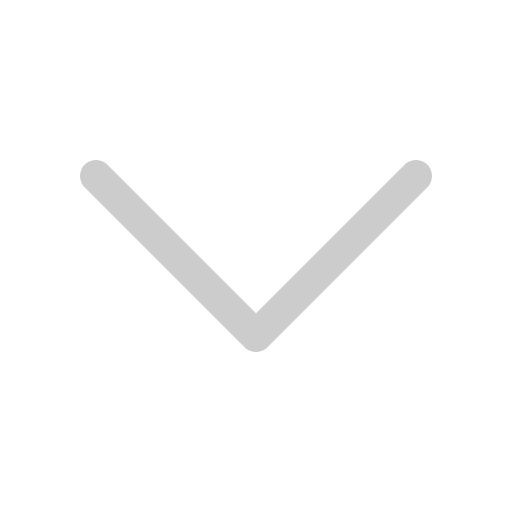
Do you have minimum order quantities?
Dynamic has a $100 minimum order quantity and many of our parts have individual pack minimums.
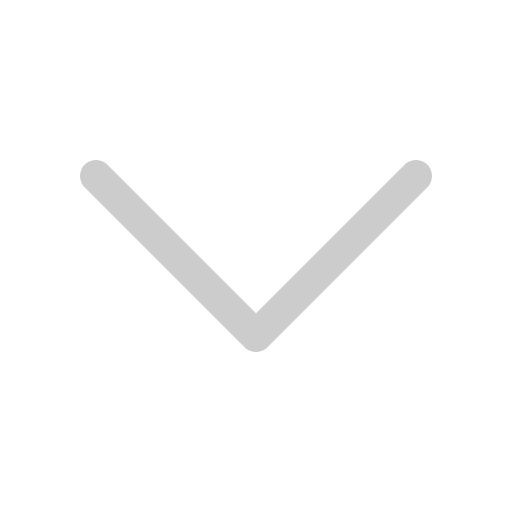
How can I purchase your products?
If you already have a preferred distributor, we suggest starting with them to find what you’re looking to purchase. If you don’t have a preferred distributor, fill out this form and we will connect you with the right fit.
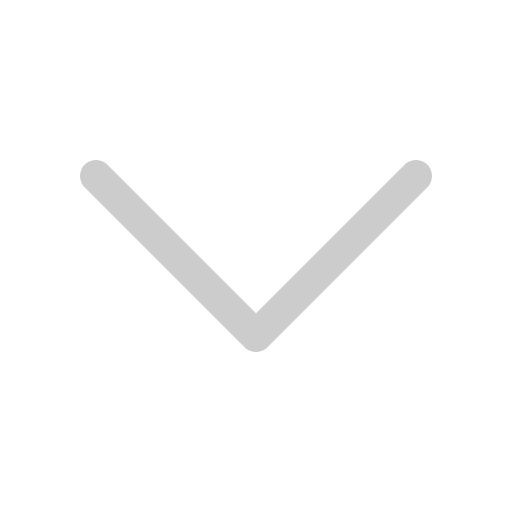
We are a small independent shop that just open and looking for a supplier for the shop. How do we purchase?
To make sure we send you to the right supplier, please contact by email at CustomerService@JohnDow.com, call us at 1-800-433-0708, or fill out this form.
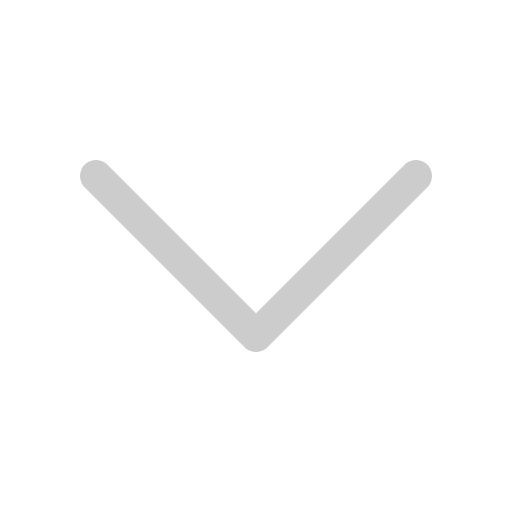
Why would I replace the cap?
The cap contains a rubber seal preventing moisture and dirt from entering the stem and contaminating the seal of the valve core. The cap is an integral component in the sealing system of the TPMS sensor and should be replaced together with the rest of the components in the service pack at each tire change.
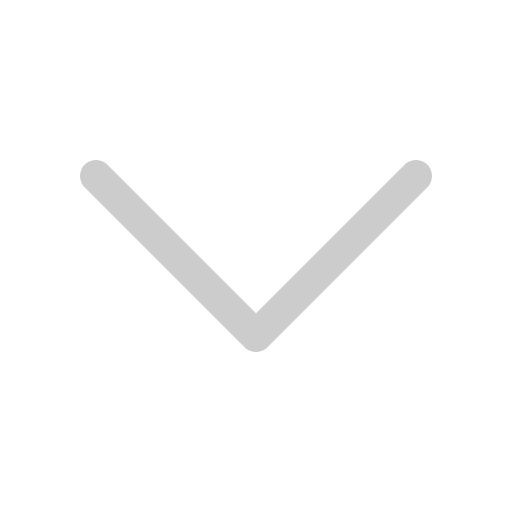
Why would I replace the valve core?
Heat and compression will eventually cause deterioration of rubber and plastic components. Replacing the valve core is vital to prevent slow leaks. Do not re-use a valve core. Replace with a new electroless nickel plated valve core for aluminum valves with each tire change.
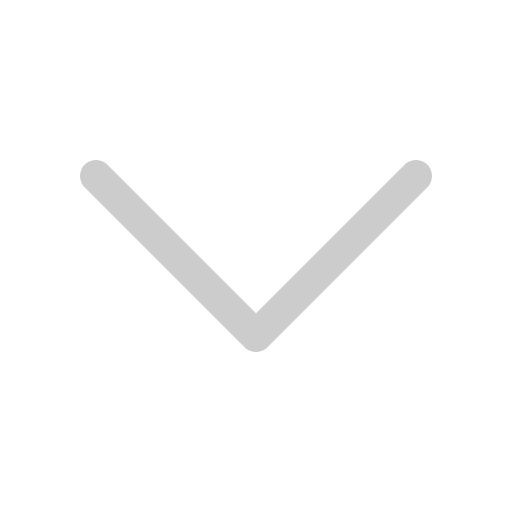
Why would I replace the nut (for clamp-in sensors only)?
The anodized aluminum nut prevents metals from the possibility of galvanic corrosion. You should only use nickel-plated valve cores on aluminum valve stems. Additionally, torquing and retorqueing the nut multiple times may damage the threads to the point of failure. A new nut ensures accurate torquing.
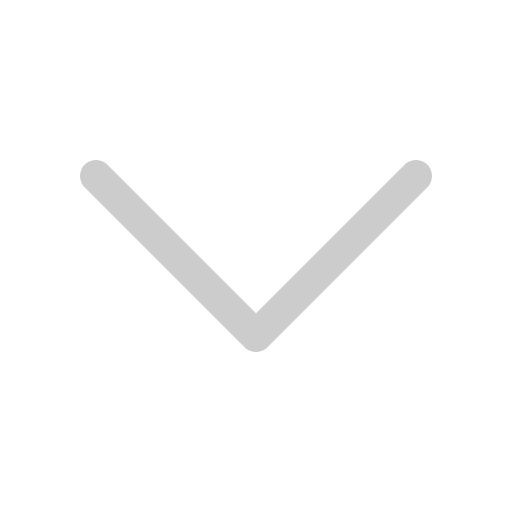
Why would I replace the rubber valve (for snap-in sensors only)?
Since the rubber valve is constantly exposed to various environmental and weather conditions, it will inevitably experience more wear and tear along with aging. Replace the valve evert every time you change the tires. changed.
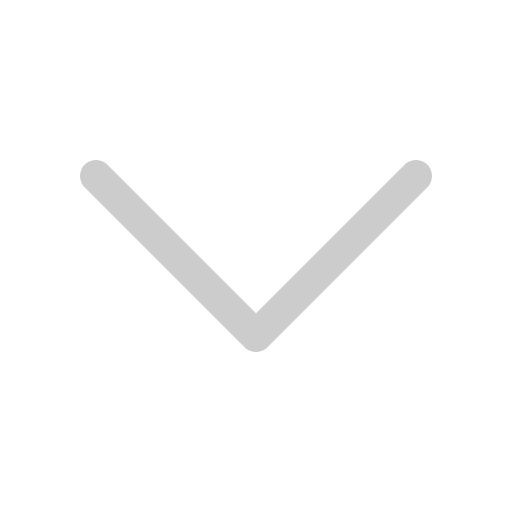
Why would I replace the grommet (for clamp-in sensors only)?
The grommet – the sealing gasket between the stem and the wheel rim hole – is subject to intense compression and high temperatures causing the grommet to adapt its shape to the rim surface. For a secure air seal, replace the grommet together with the other components in the service pack at each tire change.
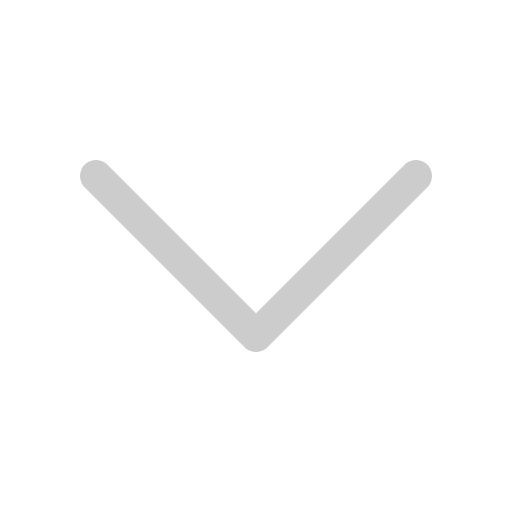
Why would I replace the valve screw?
The valve screw is a self-tapping threaded screw that connects the valve to the sensor body to ensure a secure connection. The screw cannot be used a second time, so you will need to replace the screw.
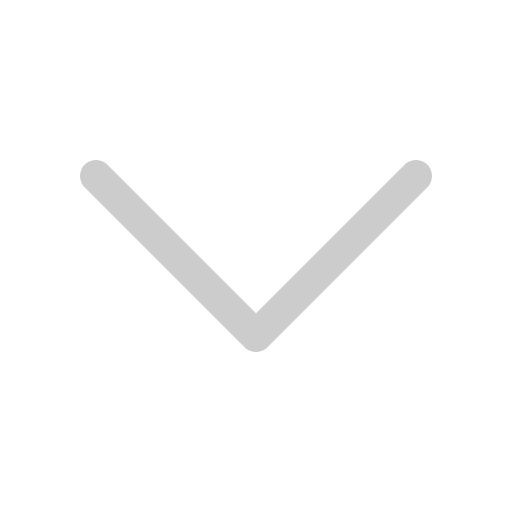
What if the DVT Pro-Select sensor is incorrectly programmed and installed in the tire?
The DVT Pro-Select and DVT-PRO can simply be reprogrammed right through the tire.
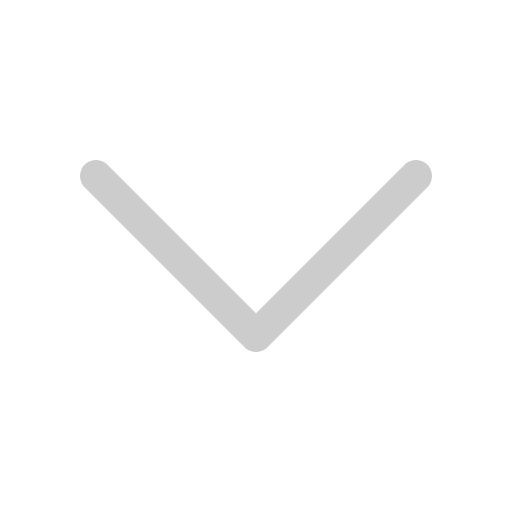
What is a TPMS rebuild kit?
A TPMS rebuild kit contains all the components to rebuild the TPMS sensor’s valve. Replacement is recommended any time your tires/TPMS receive service. A rebuild kit includes:
- Hex Nut
- Washer(s)
- Valve Core
- Rubber Grommet
- Plastic Valve Cap
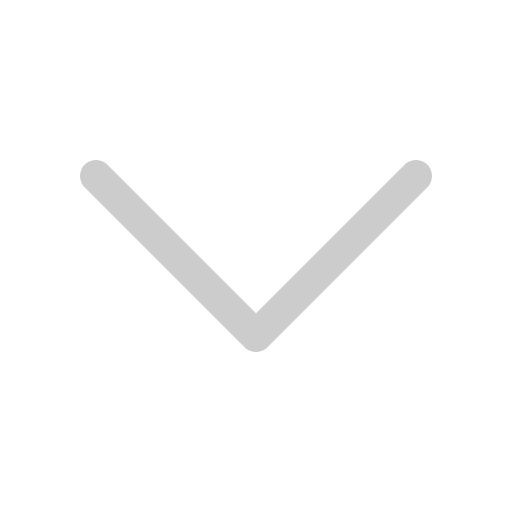
My TPMS stem is corroded but the sensor still works. Can I replace just the stem?
- If you have a 1-piece style sensor, you cannot replace the stem.
- If you have a 2-piece style sensor, you can replace the stem and can service the sensors with a rebuild kit.
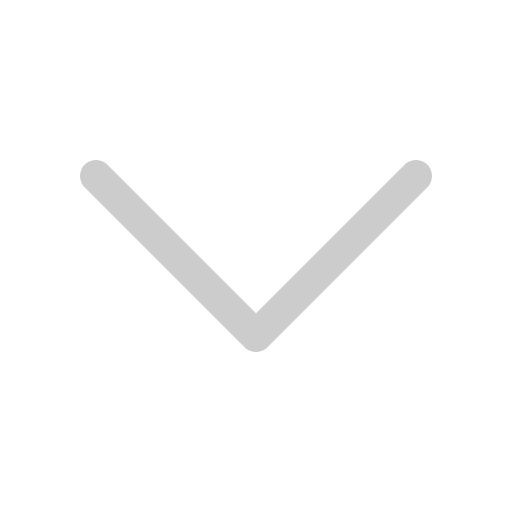
I have dark tinted windows. Will the tint interfere with the OEM relearn?
Sometimes tinted windows interfere with the OEM relearn. We recommend rolling the windows down until the OEM relearn is complete.
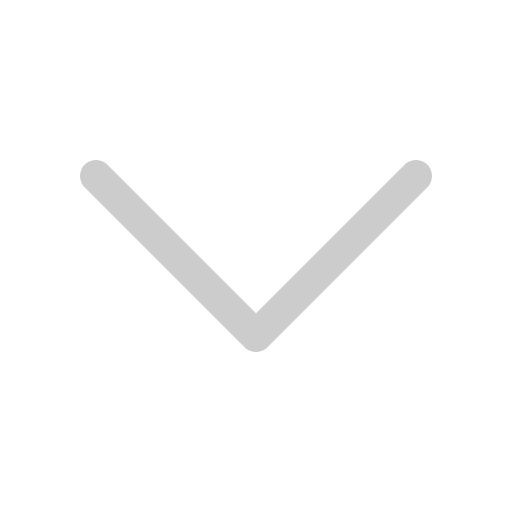
I have Bluetooth accessories installed in my car. Will those accessories interfere with the OEM relearn?
Sometimes Bluetooth devices will interfere with the OEM relearn. We recommend unplugging these devices until the OEM relearn is complete.
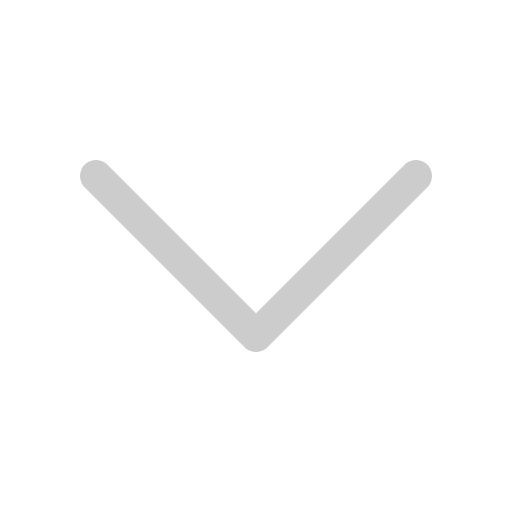
Can aftermarket accessories interrupt the TPMS signal or prevent it from communicating with my vehicle?
Absolutely. Large custom wheels, metallic window tint, certain wireless and/or Bluetooth devices and even a plug-in charger can block the signal creating a constant or intermittent system fault.
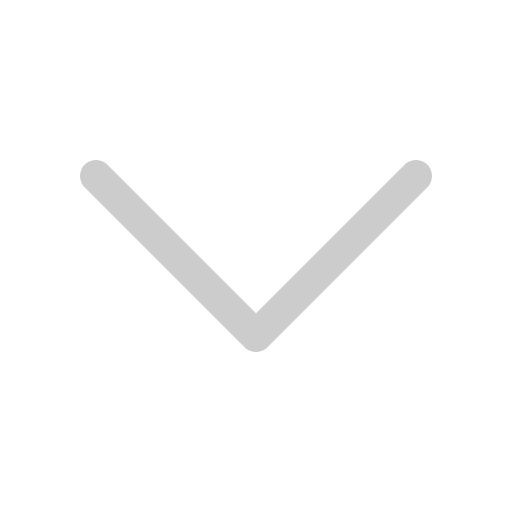
I need help!
Give our Dynamic Tech Support a call Monday – Friday 8 a.m. – 5 p.m. ET. at 1.800.805.4058.
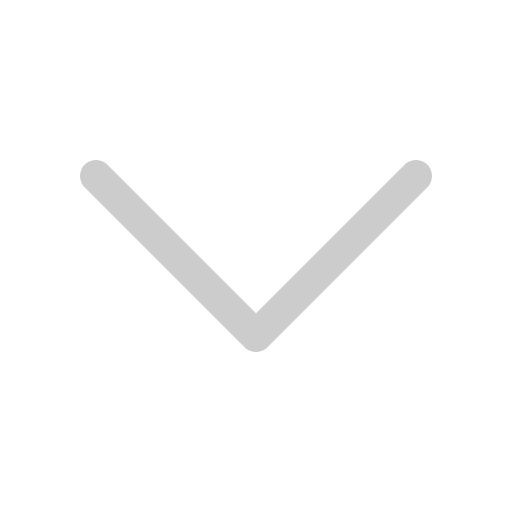
How do I program sensors?
Using one of many supported TPMS programming tools, select: YEAR – MAKE – MODEL & Dynamic. The tool will instruct which DVT sensor to use. The tool will program the sensor(s) based on your vehicle. Finish any installation needed, and perform the OE relearn (see the Application Guide for the specific procedure).
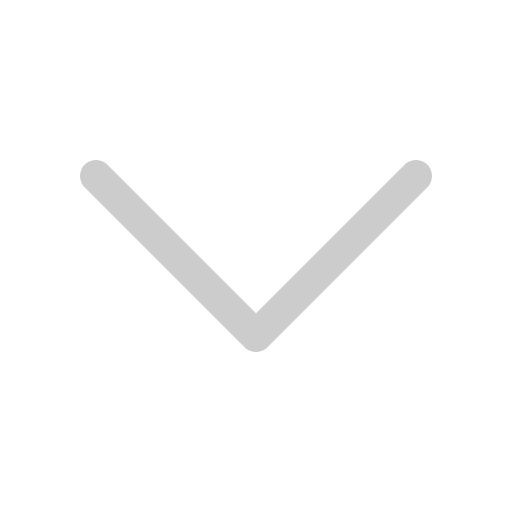
Can I simply replace the battery?
No! The battery cannot be replaced. The housing is sealed to protect internal components, so always replace the entire sensor and never just the battery.
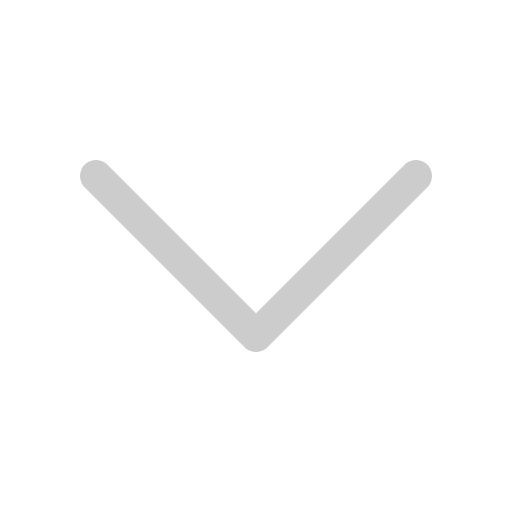
What do I do with the old sensors?
You can dispose of them properly. Make sure to dispose the old sensors at least 100 feet from the vehicle to prevent interference during the relearning of your new sensors.
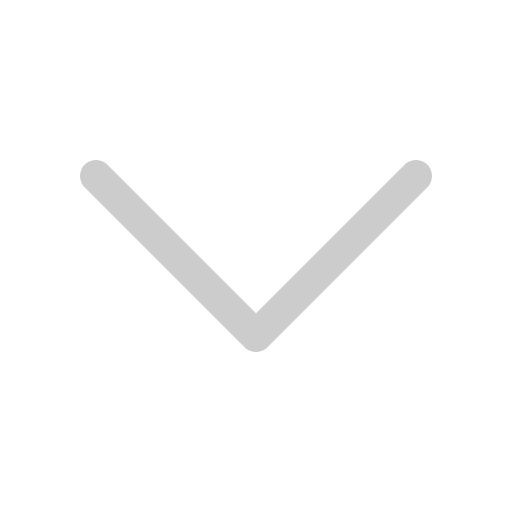
Can I bypass or disable the TPMS system?
No. Under 49 U.S.C. 30122(b), “A manufacturer, distributor, dealer or motor vehicle repair business may not knowingly make inoperative any part of a device or element of design installed on or in a motor vehicle or motor vehicle equipment in compliance with an applicable motor vehicle safety standard.”
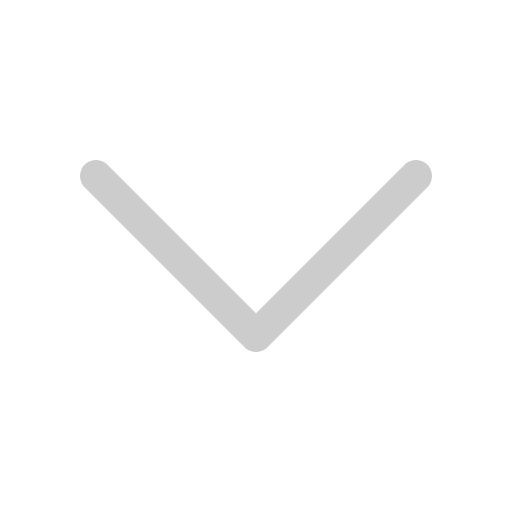
I replaced my TPMS sensors, and I finally have working sensors, but the registered PSI number is about 3 PSI low on three accurate tire gauges. Is this normal?
Your vehicle dashboard gives you an accurate pressure reading while your shop gauge displays a relative pressure. A conventional shop gauge may display different results based on environmental factors like altitude and weather. The TPMS Pressure Gauge will always display the exact PSI it receives from the sensor inside the tire.
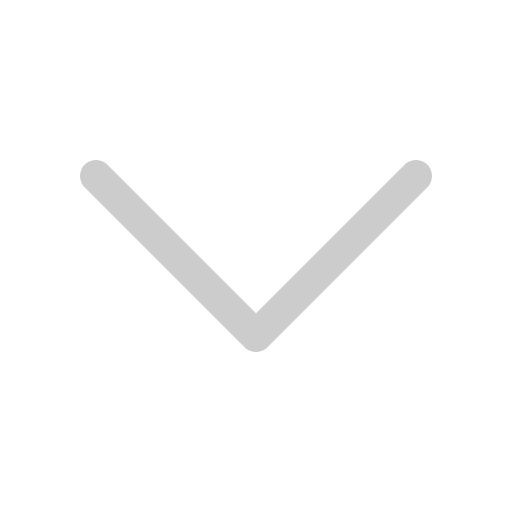
My car has TPMS. I haven’t had it serviced yet at my repair facility. What should I expect when I get there?
You should expect the following:
- Service or replacement of any nonfunctioning component of your TPMS sensors
- Replacement of TPMS sensor sealing components (cap, core, grommet and nut)
- A “relearn” of your TPMS sensors to your vehicle’s computer to program correct positioning of TPMS sensors
- Verification that your TPMS system is functioning properly after tire service is complete
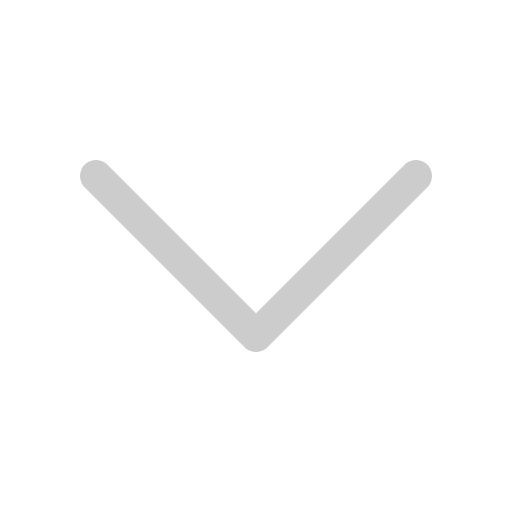
Where do I find my vehicles recommended Pounds Per Square Inch (PSI)?
To identify your vehicle’s recommended PSI, check the tire placard. The tire placard is an informational label put on your vehicle by the original equipment manufacturer, normally located inside the driver’s side door frame or doorpost. It may also be on the edge of the driver’s door or the inside of the glove box door or trunk lid. It contains information including the vehicle manufacturer’s recommended tire pressure for your vehicle, the recommended tire size, and the maximum load you should have in your vehicle. This information is also located in your owner’s manual.
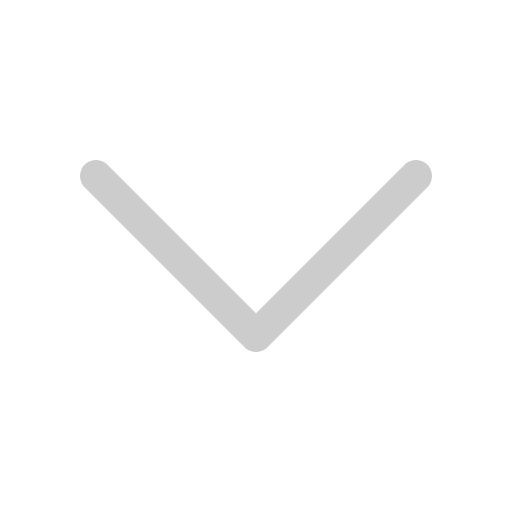
Why does tire pressure change?
Many factors affect tire pressure including ambient temperature changes and tire damage, like a puncture. Tire pressure drops about 1 PSI for every 10°F drop in ambient temperature. Additionally, tires can lose as much as 1.5 PSI per month as air escapes the tire and rim naturally.
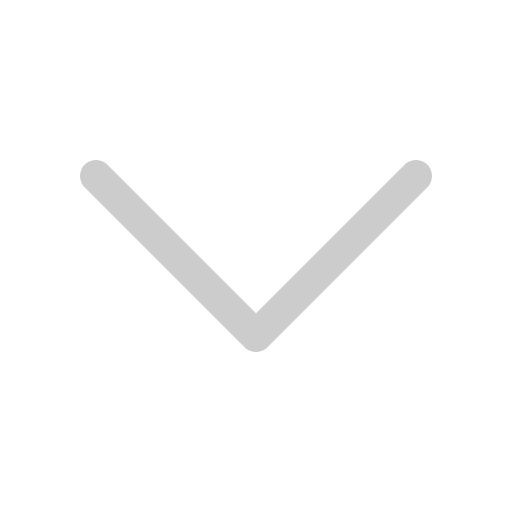
What does an under inflated tire look like?
You cannot always tell if a tire is under inflated simply by looking, kicking, or pressing on the tire. The only way to accurately check tire pressure is by measuring the tire pressure with a quality pressure gauge.
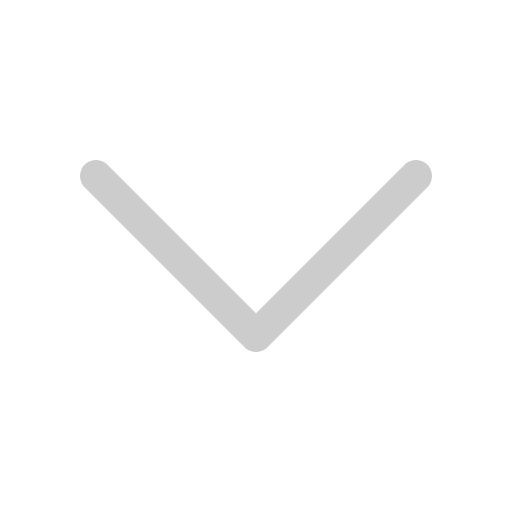
How does weather and temperature affect tire pressure?
Winter tires can wear out if used in prolonged hot conditions, and summer tires have lower resistance in slippery conditions. Customers who invest in seasonal tires will likely ask you when they need to change from their winter tires to their summer tires (and vice versa).
The magic number is 45°F. When temperatures are consistently above that mark, drive on summer tires. When temperatures are regularly below that mark, make the switch to winter tires. During each changeover, a technician should check the TPMS valves and sensors on all of the tires.
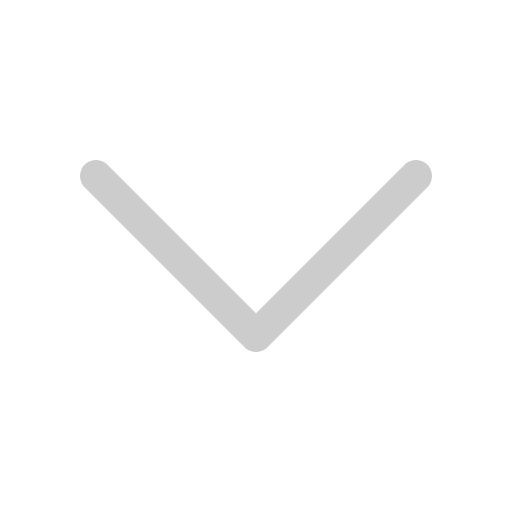
How often should I check my tire pressure?
A tire doesn’t have to be damaged or punctured to lose air. All tires will lose air naturally over time, so it’s recommended to check the pressure in all your tires, including the spare, at least once per month. Road conditions, weather conditions or other circumstances may warrant checking the pressure more often. Remember to always use a quality tire gauge when checking tire pressure, and don’t forget the spare! It may not have TPMS but check the pressure anyways in case you need your spare for an emergency.
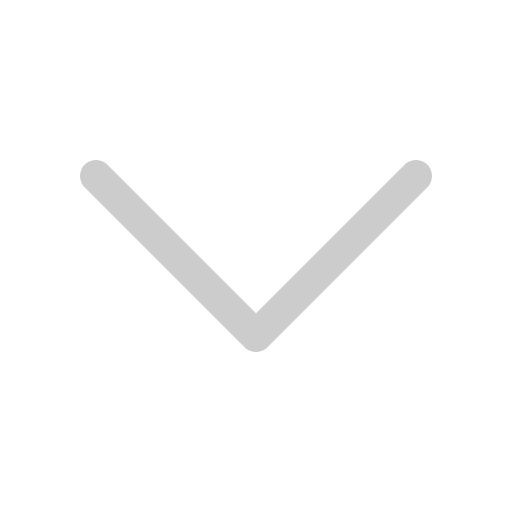
My warning light keeps coming on. What does that mean?
The TPMS warning light will illuminate if your vehicle’s tire pressure is too low or part of the TPMS system malfunctioned in any of your wheels. The light will do one of two things:
- A blinking light means the TPMS is malfunctioning. One or more sensors may have failed or lost communication. Sensor failure may occur due to a dead battery (sealed inside the sensor), damage, or from natural wear and tear. Most sensors last 8 – 10 years.
A solid light means one or more tires is operating at an unsafe pressure. Check your tires immediately.
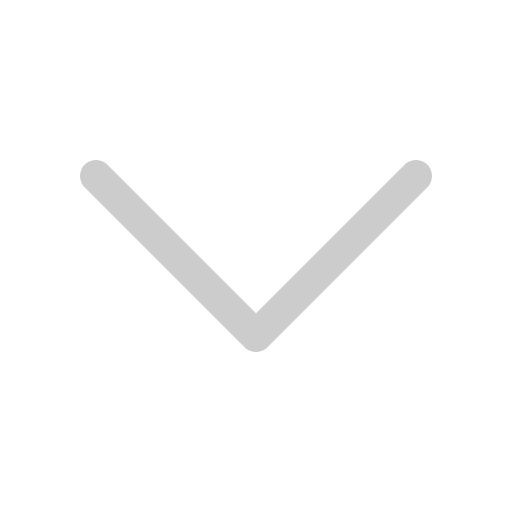
What are the benefits of TPMS?
TPMS provides safety and economic benefits. TPMS monitors the air pressure in a tire and sends a warning to the vehicle’s on-board monitoring system (on the dashboard) when the pressure drops below a preset limit. By helping drivers maintain proper tire inflation, TPMS can help improve ride and handling, reduce stopping distances and the potential for hydroplaning, increase miles per gallon, and extend tire life.
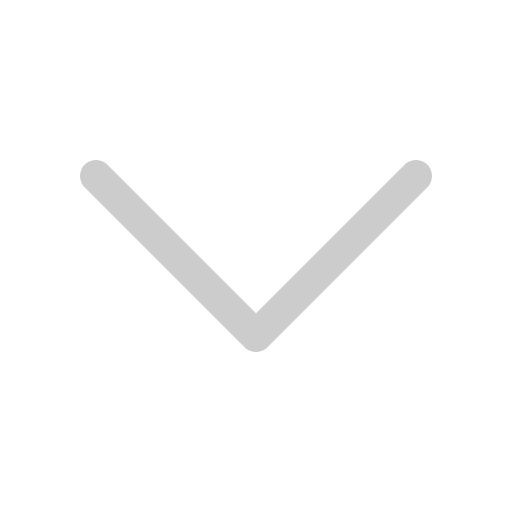
Why do I have TPMS in my Vehicle?
As of 2007, the United States Department of Transportation (through NHTSA) requires a Tire Pressure Monitoring System to all new passenger cars, multipurpose passenger vehicles, trucks, and buses that have a gross vehicle weight rating of 10,000 lbs. or less (except those vehicles with dual wheels on an axle). The legislation requiring TPMS passed in reaction to Congressional hearings on vehicle rollover deaths caused, in part, by vehicles with under inflated tires.
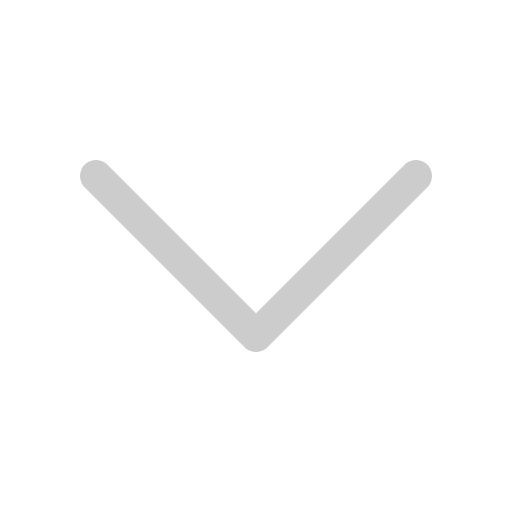
What is Tire Pressure Monitoring System or (TPMS)?
A Tire Pressure Monitoring System, or commonly referred to as TPMS, is to warn you of at least one or more tires are significantly under-inflated, possibly creating unsafe driving conditions. This indication is made on the dashboard in the form of an ICON or other warning, or both.
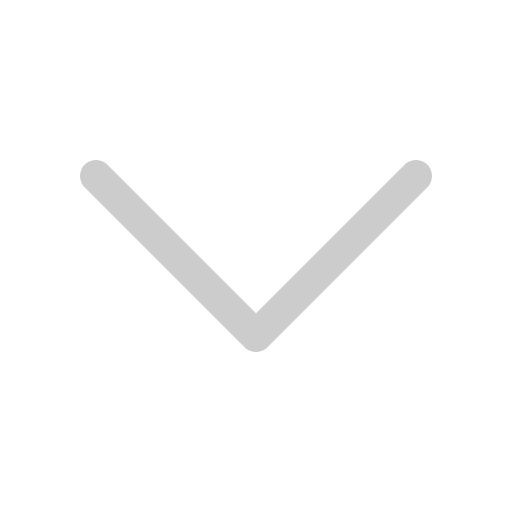
Do you have a warranty on your products?
JohnDow Dynamic back shop supply and TPMS products which prove to be defective in material and workmanship within one (1) year from the date of purchase may be returned freight prepaid for repair, replacement or credit at the discretion of JohnDow personnel. If JohnDow inspection discloses no defect in material or workmanship, repair, replacement or return will be made at customary charges This warranty does not cover failure of parts or components due to normal wear or damage, wear which in the judgment of JohnDow arose from misuse, abrasion, negligence, accident, faulty installation, or tampering.
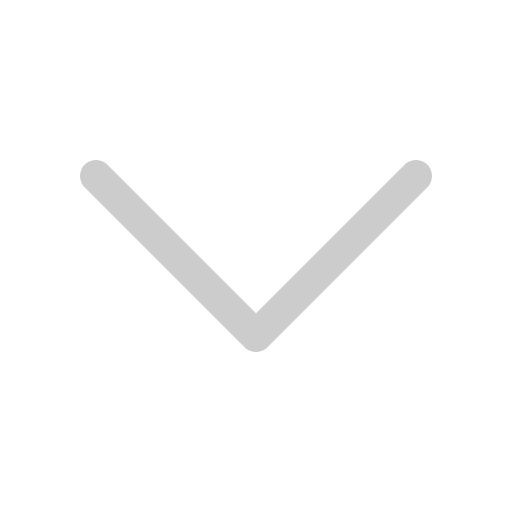
I have a technical question. Who can I talk to?
The experts on our technical team is well-versed in all of our products. If you have a technical question, you can email us at CustomerService@JohnDow.com, call us at 1-800-433-0708, or fill out this form.
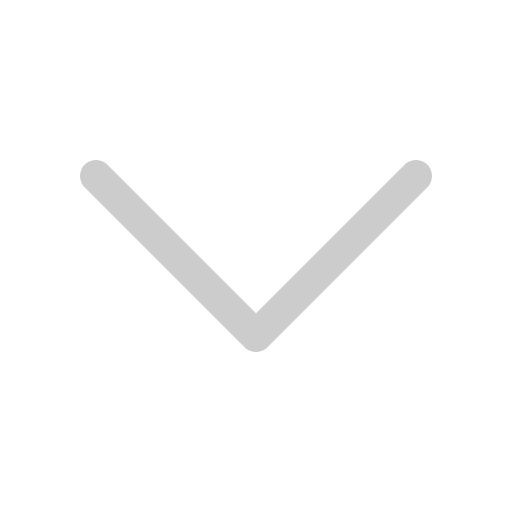
Where can I find SDS sheets?
You can find all of our chemical SDS sheets on our website, JohnDow.com under About Us > SDS Sheets.
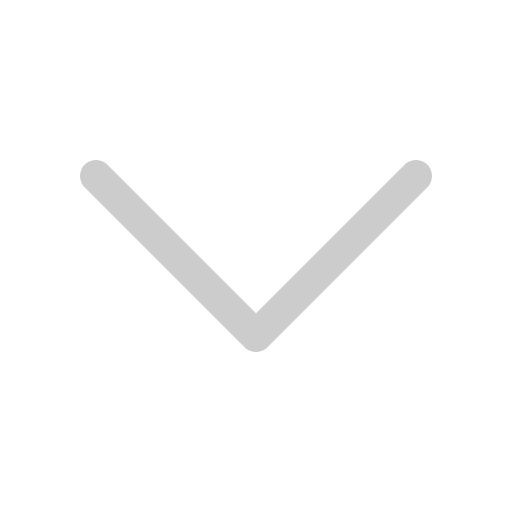
Do you have an application guide?
We have a TPMS, Wheel Hardware and Drain Plug Application Guide to provide technicians with Year-Make-Model (Y-M-M) lookup information for Dynamic wheel studs, wheel nuts, drain plugs, gaskets and TPMS
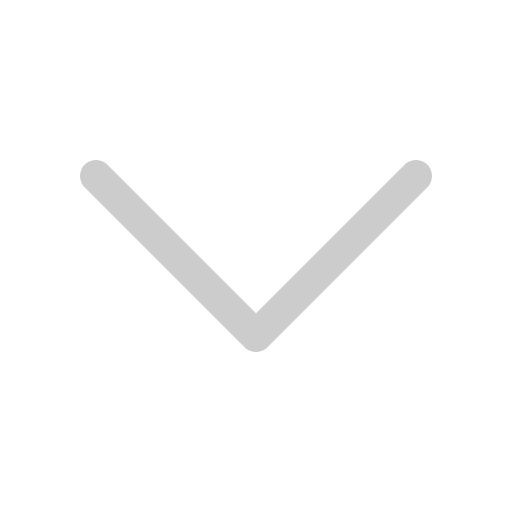
How can I find a part for a specific vehicle?
You can find or Wheel Nut/Studs, Drain Plugs/Gaskets and TPMS application parts by Year, Make, Model using our Application Search. on our www.johndow.com/dynamic website.
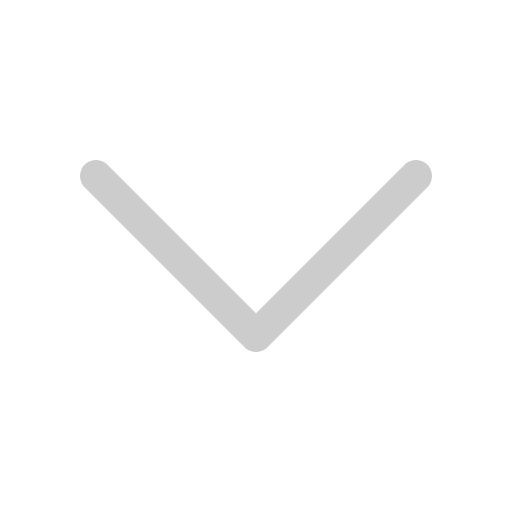
Do you have minimum order quantities?
You can find all of our product offerings through popular automotive supply distributors. If you already have a preferred supply distributor, we suggest starting with them to find what you’re looking to purchase. If you don’t have a preferred distributor, fill out this form and we will connect you with the right fit.
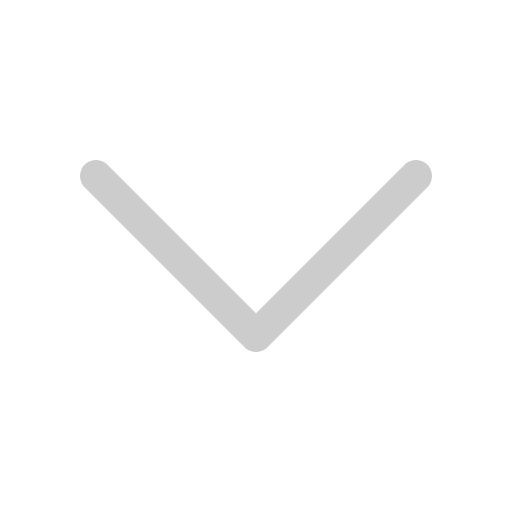
What shop supplies do you sell?
Our automotive service parts and shop supplies include the following categories:
- Brake Service Parts
- Fuel Lines & Fittings
- Oil Drain Plugs & Gaskets
- Wheel Hardware
- Electrical Hardware
- Wheel & Tire Supplies
- Automotive Hardware
- Automotive Service Chemicals
- Automotive Interior Protection
- Storage Solutions
- Boxed Service Parts
- TMPS Sensors, Service Kits & Accessories
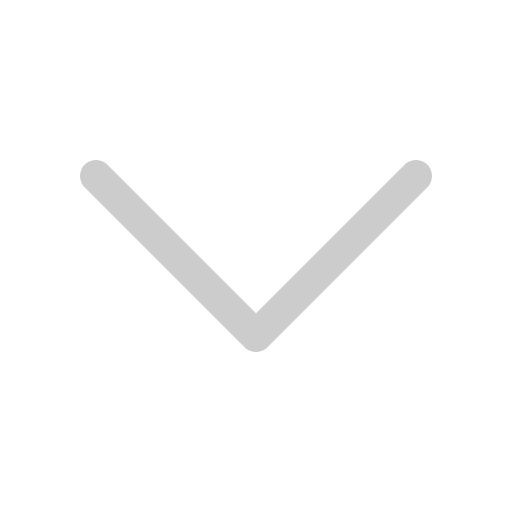
What chemicals do you carry?
We carry nearly 40 different chemicals under the following:
- General shop aerosol products
- Brake service products
- Instant gasket products
- Warranty seal
- Lubricants & Cleaners
- Power steering fluid
- Tire care products
- Tire service products
- Janitorial products
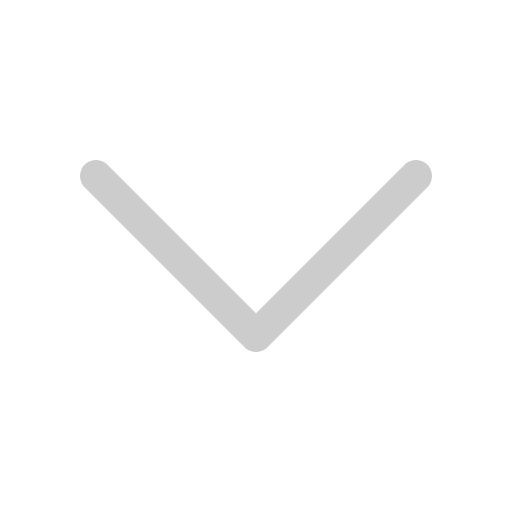
Do you carry tire-related parts?
Yes, we carry the following supplies for tires:
- TPMS products
- Brake service parts
- Wheel hardware
- Wheel & Tire Supplies
- Service chemicals
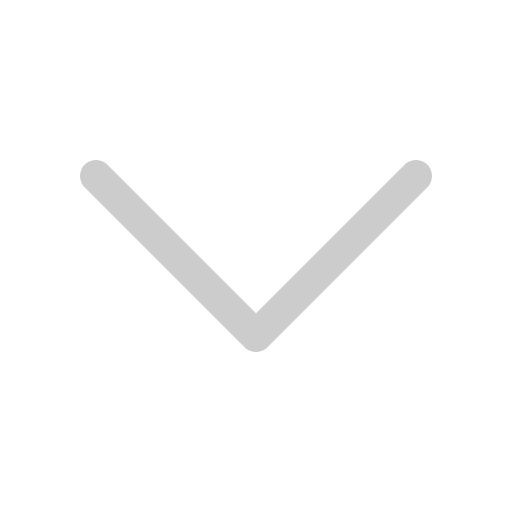
Do you carry auto parts?
We offer repair parts in the following categories:
- TPMS products
- Brake service parts
- Wheel hardware
- Wheel & Tire Supplies
To see a full list of all of our repair parts, click here.
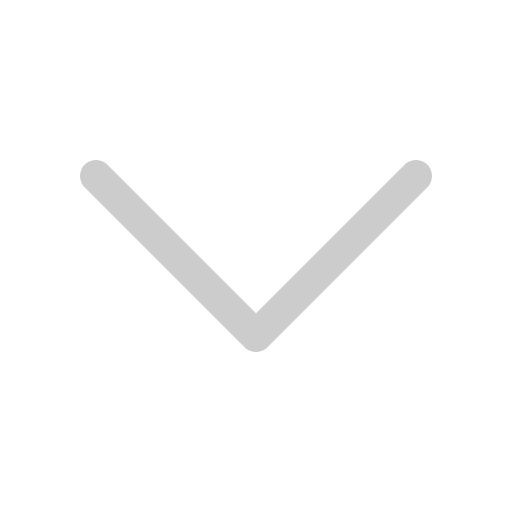
What kind of supplies do you carry?
We carry the following automotive service parts and shop supplies:
- Brake Line Coils & Fittings
- Fuel Lines & Fittings
- Oil Drain Plugs & Gaskets
- Wheel Nuts & Studs
- Electrical Hardware
- Wheel & Tire Supplies
- Automotive Hardware nuts, bolts, and hose clamps
- Automotive Service Chemicals
- Automotive Interior Protection
- Storage Solutions
- Boxed Service Parts
- TPMS Sensors, Service Kits & Accessories
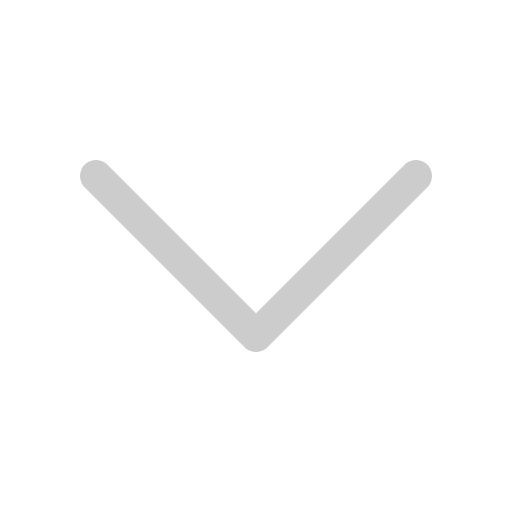
Do you sell direct?
You can find all of our product offerings through popular automotive supply distributors. If you already have a preferred supply distributor, we suggest starting with them to find what you’re looking to purchase. If you don’t have a preferred distributor, fill out this form and we will connect you with the right fit.
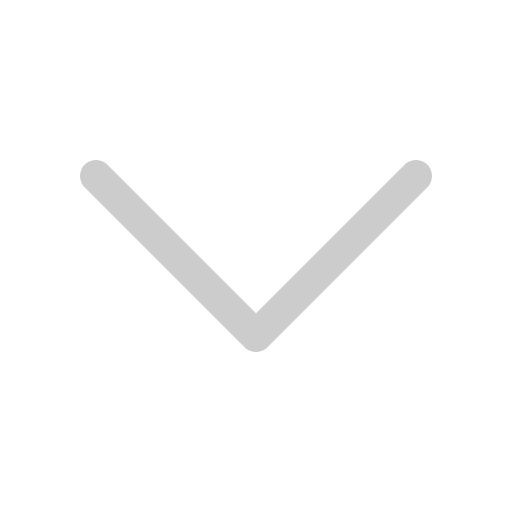
How can I purchase your products?
If you already have a preferred distributor, we suggest starting with them to find what you’re looking to purchase. If you don’t have a preferred distributor, fill out this form and we will connect you with the right fit.
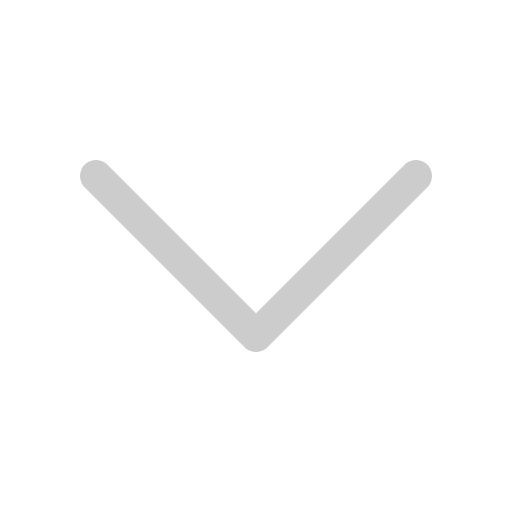
We are a small independent shop that just open and looking for a supplier for the shop. How do we purchase?
To make sure we send you to the right supplier, please contact by email at CustomerService@JohnDow.com, call us at 1-800-433-0708, or fill out this form.
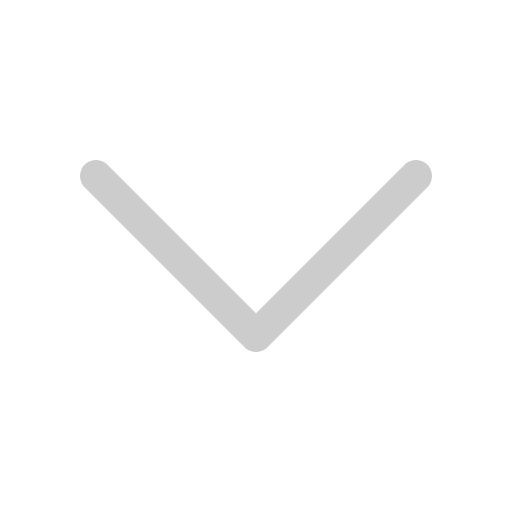
Are EuroVent products made in the USA?
All EuroVent Exhaust Extraction Systems conform to the Buy American Act. We engineer and assemble all products in our Barberton, Ohio manufacturing facility following a 100-page instruction and quality testing process before shipping.
Assembly in the USA allows installment of our custom systems for any government repair facilities, including military, municipal, aircraft, construction, and heavy-duty.
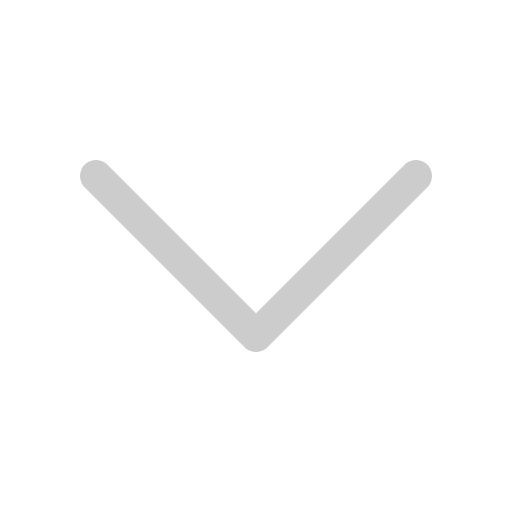
Do you have a warranty on your products?
Yes! EuroVent exhaust extraction products (except aluminum rail and neoprene seal) which prove to be defective in material and workmanship within one (1) year from the date of purchase are returnable with freight prepaid for repair, replacement or credit. If the fan and/or motor was not installed per the manufacturer’s drawing, the fan and/or motor warranty may be void.Limited Lifetime Warranty – Aluminum Rail & Neoprene Seal
JohnDow warrants the rail and neoprene seal is free from defects in materials and manufacture for as long as the original purchaser owns the system. The warranty does not include normal wear and tear or failure to misuse, carelessness or any accidental cause.
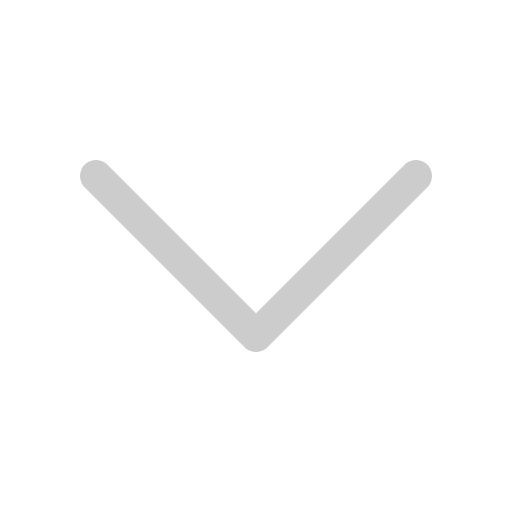
Do these systems fit every vehicle? Are there adapters?
We have several different accessories and adapters to fit any vehicle exhaust system.
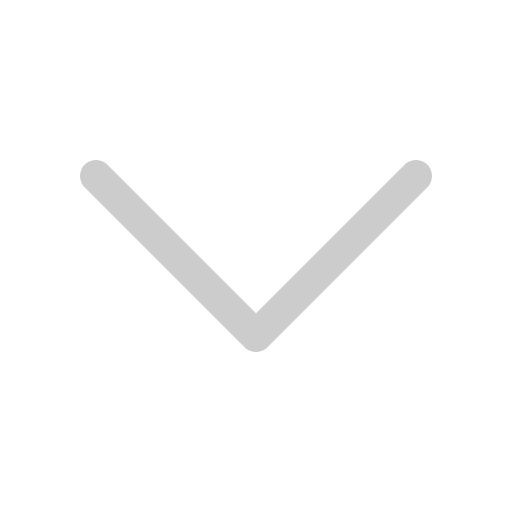
Do heavy-duty vehicles require a different type of system?
Yes. Heavy-duty vehicles need larger systems and must withstand higher temperatures. To better understand what system could work for you, please contact us.
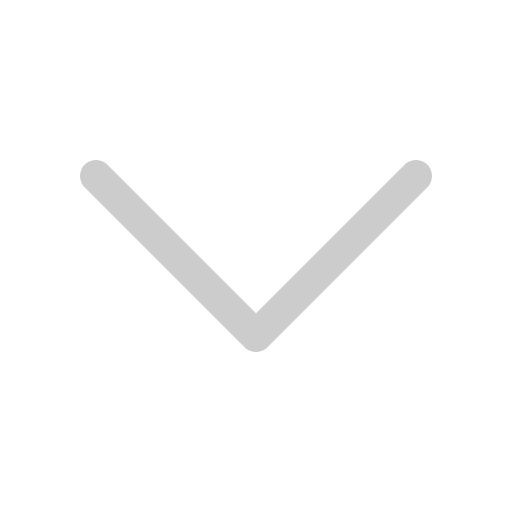
Do diesel vehicles require a different type of system?
Yes. Diesel systems are larger and withstand higher temperatures. To better understand what diesel system could work for you, please contact us.
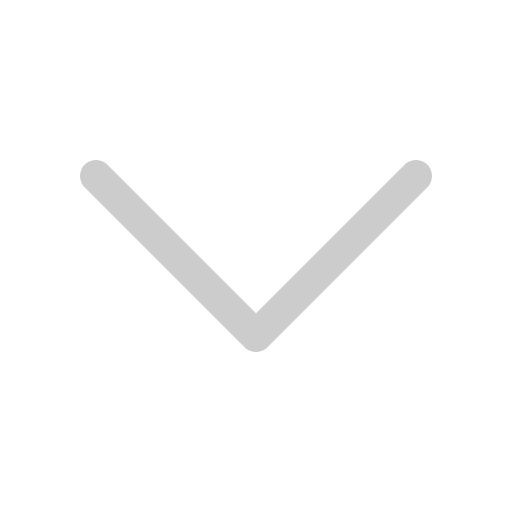
How do I get replacement parts?
Please contact us if you are having any issues with your exhaust extraction system. We can help coordinate replacement parts for your system, if needed.
All orders must take place through an authorized EuroVent distributor or sales representative.
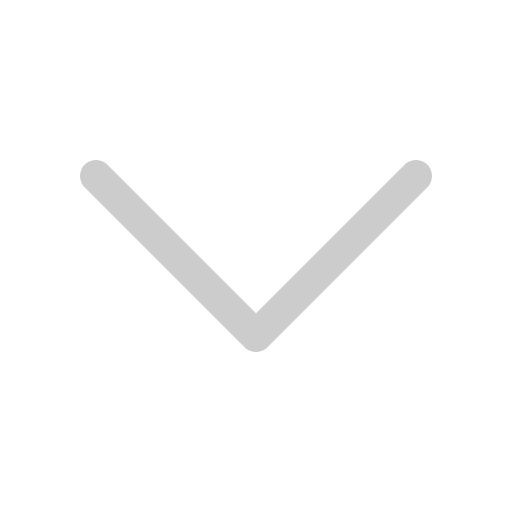
Do you sell direct?
No. We sell through equipment distributors across the country because of their expertise and project installation. Please contact us and we can provide you with a local distributor specific to your project.
All orders must take place through an authorized EuroVent distributor or sales representative.
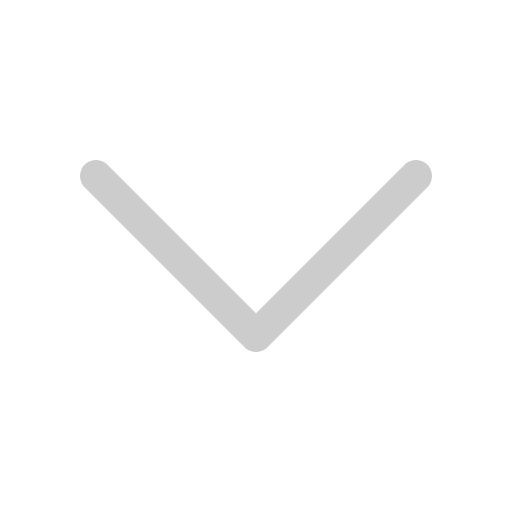
Do I need drawings of my facility for a quote?
Yes. Following your initial inquiry, we will work with you to gather all details for the type of system and requirements you’re looking for. From CAD or other drawing provided by your contractor, architect, HVA contractor or another source, our engineers will calculate the performance parameters of the system. Within five (5) days, we will provide a design package that fits your facility’s specific requirements, budget and timetable.
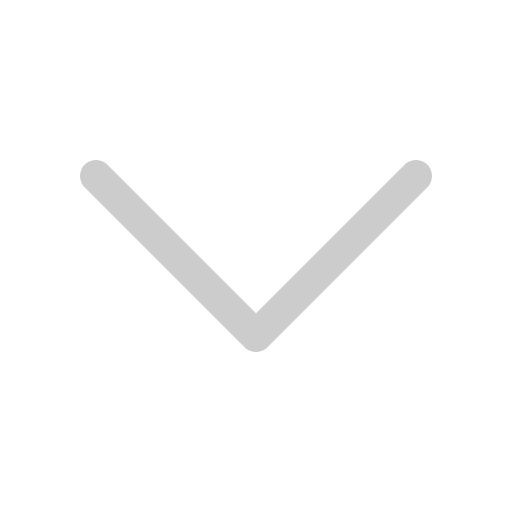
How do I submit a request for quote?
We will need your drawing and system requirements to get started on a quote for you, but first contact us or call 1-800-433-0708. Visit our Quoting Process page to understand how it works.
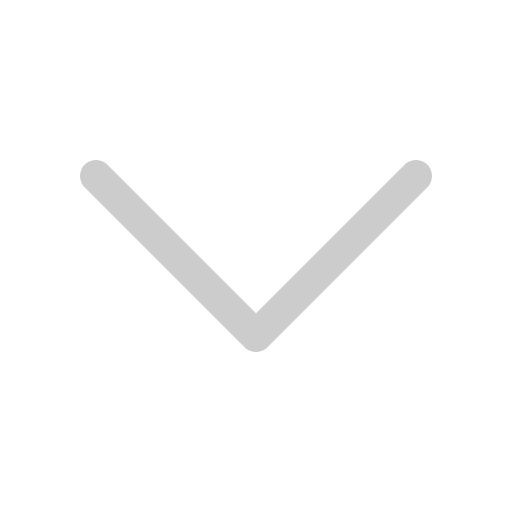
If I am interested in getting a EuroVent system. How do I get started?
Contact us or give us a call at 1-800-433-0708 and we can help you get started.
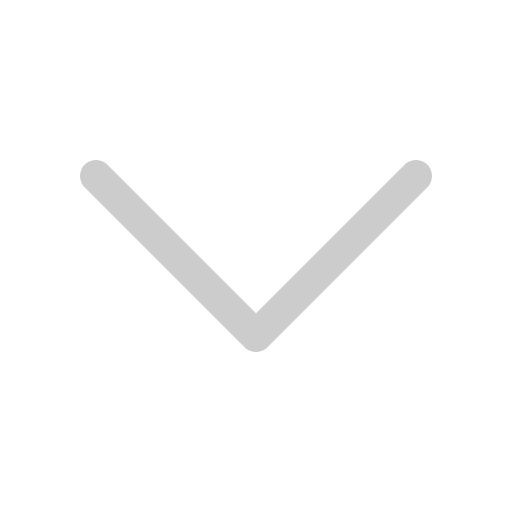
What types of extraction systems are there?
There are many different types of exhaust extraction systems, and we will always recommend a system that works best for your facility. We offer:
- Overhead rail exhaust systems including:
- Sliding crab hose reels & drops
- Fixed Hose Reels
- Motorized Hose Reels
- Fixed telescoping hose drops
- In-ground exhaust systems
- Portable exhaust extraction systems
- Out-the-door exhaust extraction systems
- Exhaust Fans
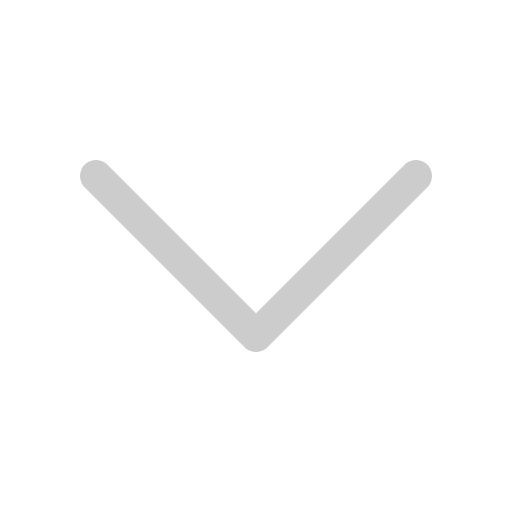
How expensive are vehicle exhaust extraction systems?
This depends on a lot of variables including your facility size, vehicles you service, type of exhaust system you choose to install, etc. To get a better understanding of what your project would cost with your facility specifics, please contact us.
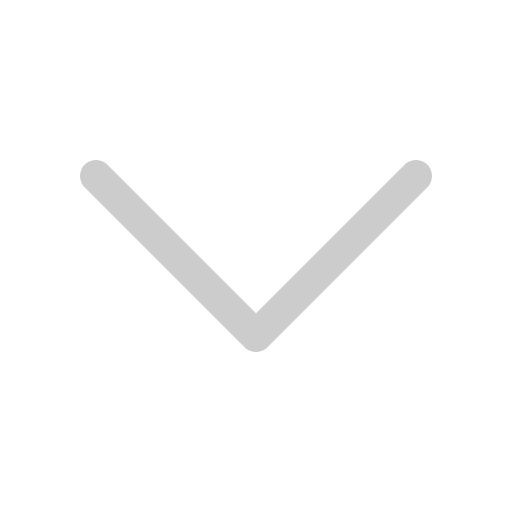
Why do I need a vehicle exhaust extraction system? Can’t I just open a door?
You can open a door if you are working on a vehicle near a garage door, but often repair facilities have too many bays for this to be feasible, safe, and healthy.
A properly designed and installed vehicle exhaust extraction system will guarantee the removal of harmful exhaust fumes as well as reduce energy consumption and air loss.
We professionally design EuroVent systems using the latest industry criteria to provide a safe work environment for employees, ensure compliance with local regulations and minimize air make-up requirements. To avoid potential noise-inducing hearing loss, all of our systems operate below 85 dBA, the rate at which long or repeated exposure to sounds can cause hearing loss. We live by, and strictly follow OSHA Indoor Air Quality (IAQ) standards, and ASHRAE ventilation standards so your healthy work environment will increase productivity and retain talented technicians.
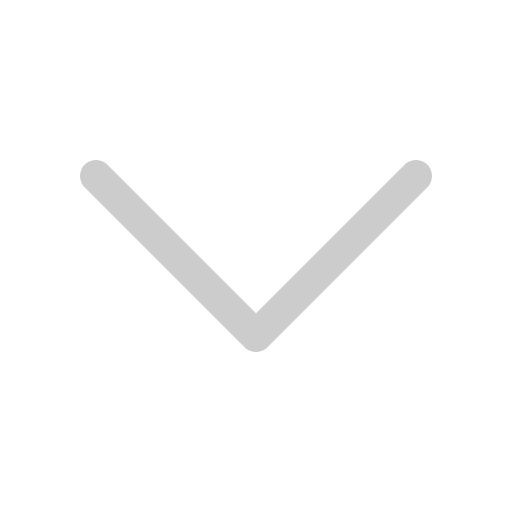
What is vehicle exhaust extraction?
Vehicle exhaust extraction systems remove harmful exhaust fumes right from the tailpipe of a vehicle.
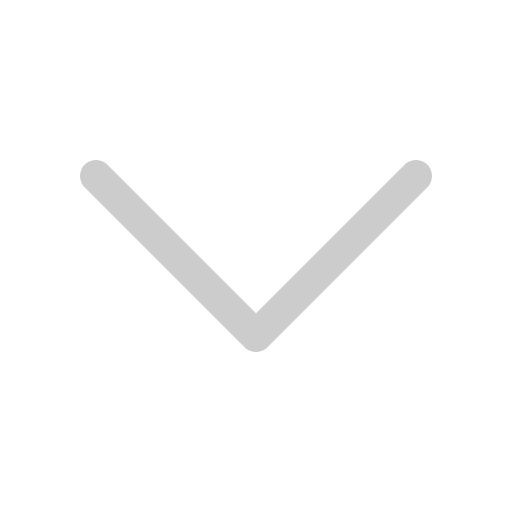
Do your grease and oil delivery systems include the drum?
No. Our grease systems come with a 50:1 high-pressure pump, control handle, z-swivel, drum cover. Follower plate, and an 8’ outlet hose. These grease systems fit 35 lb. 120 lb., and 400 lb. grease containers.Our oil systems come with a 3:1 medium-pressure pump, delivery gun, and a 10’ delivery hose. These oil systems fit on 16- and 55-gallon drums.
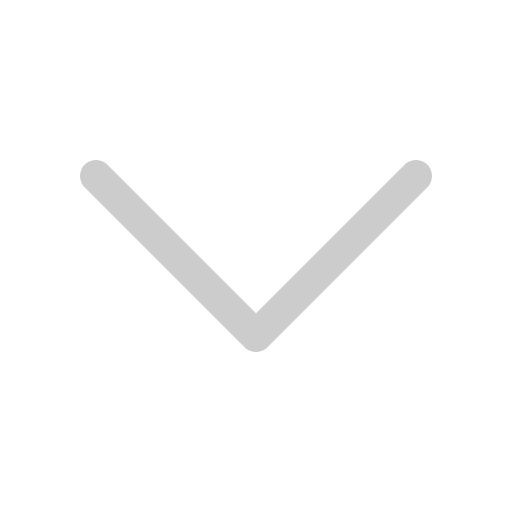
What sizes do your Aboveground Used Oil Storage Systems come in?
All JDI Aboveground Used Oil Storage Systems feature a UL Listed double-wall tank with 110% secondary containment, meets UL 142 specifications and Uniform Fire Code and NFPA 30 requirements, and come in 180-, 245-, 285-, and 500-gallon capacities.
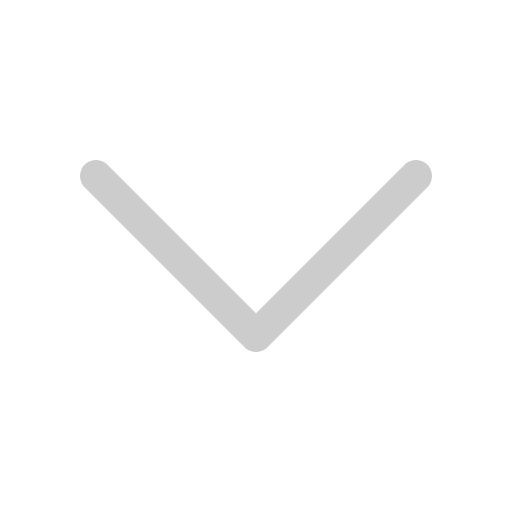
What sizes do Hose Reels come in?
Our Professional Series Hose Reels come in 50-foot lengths and come in different sizes for low, medium and high pressure applications.
Model No. | PSI Rating | Hose Size | Hose Length | Weight |
Low Pressure for Air, Water & Antifreeze | ||||
JD-3850 | 300 psi | 3/8″ | 50′ | 53 lbs. |
JD-1250 | 300 psi | 1/2″ | 50′ | 59 lbs. |
Medium Pressure for Motor Oil & ATF | ||||
JDM-3850 | 2250 psi | 3/8″ | 50′ | 53 lbs. |
JDM-1250 | 2250 psi | 1/2″ | 50′ | 57 lbs. |
High Pressure for Grease | ||||
JDH-1450 | 5000 psi | 1/4″ | 50′ | 53 lbs. |
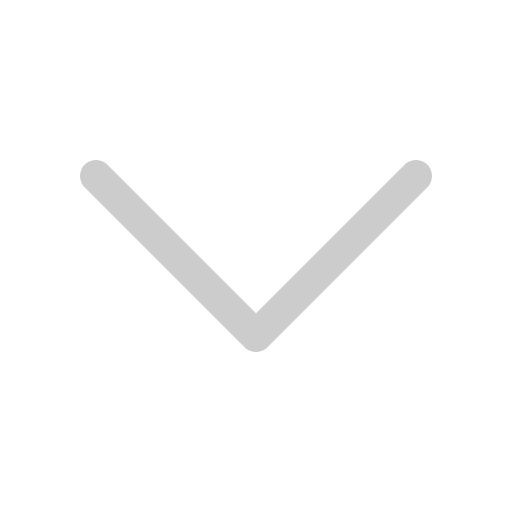
How much can a heavy-duty Tire Taxi hold?
The Tire Taxi HD measures 31.4” in diameter and can hold 5 tire and wheel assemblies or 8 tires, totaling a max load of 552 lbs.
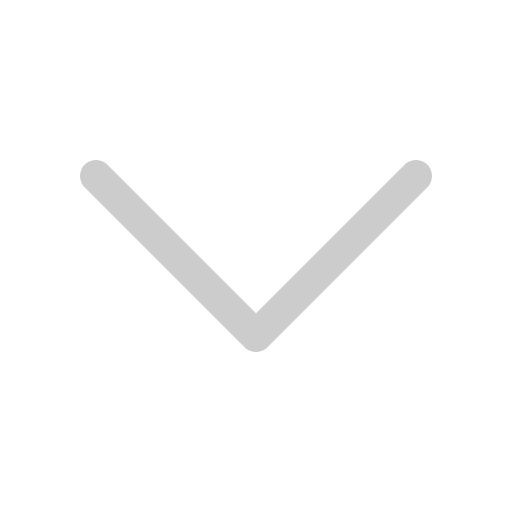
How do you crush a used oil filter?
A crushing or puncturing device is needed. The most common method is using an oil filter crusher, which removes greater than 95% of the residual oil from the filter. This makes disposal much safer for the environment.
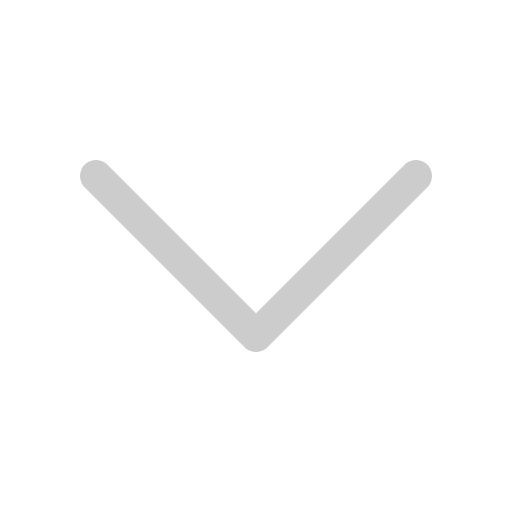
How much can a standard Tire Taxi hold?
The original Tire Taxi measures 24.5” in diameter can hold 5 tire and wheel assemblies or 8 tires, totaling a max load of 265 lbs.
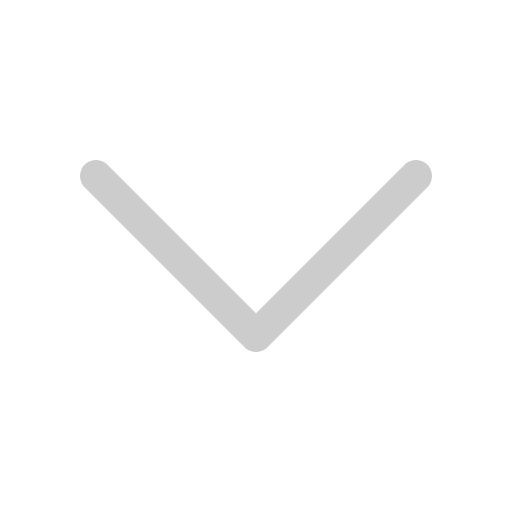
Do you have a warranty on your products?
Yes! JohnDow Service Equipment products which prove to be defective in material and workmanship within one (1) year from the date of purchase may be returned freight prepaid for repair, replacement or credit at the discretion of JohnDow personnel. If JohnDow inspection discloses no defect in material or workmanship, repair, replacement or return will be made at customary charges. This warranty does not cover failure of parts or components due to normal wear or damage, wear which in the judgment of JohnDow arose from misuse, abrasion, negligence, accident, faulty installation, or tampering.If you have a question about a specific product, please reach out to us by calling 1-800-433-0708 or fill out this form.
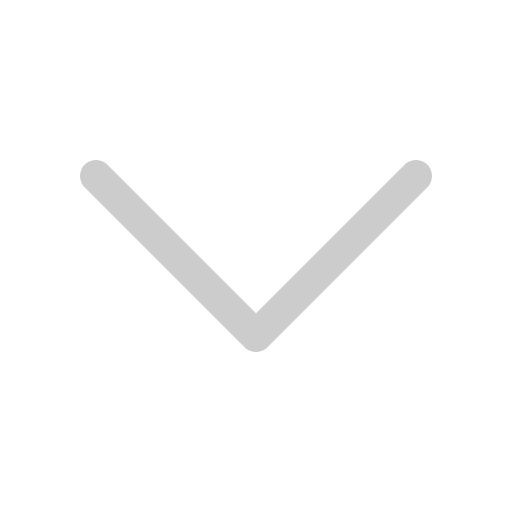
Do you carry oil drains for commercial or heavy-duty vehicles?
Yes. We offer a variety of low-profile oil drains designed for larger vehicles that range from 17- to 25-gallons in both poly and steel. These oil drains also come with manual or air-operated pump capabilities.
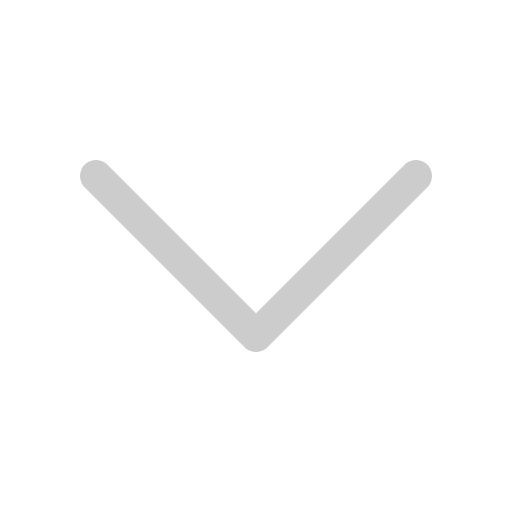
Where can I purchase an oil drain?
We work with a variety of distributors throughout the United States who sell our service equipment, both in person and online. If you already have a preferred shop supplies distributor, we suggest starting with them to find the equipment you’re looking to purchase. If you don’t have a preferred distributor, fill out this form and we will connect you with the right fit.
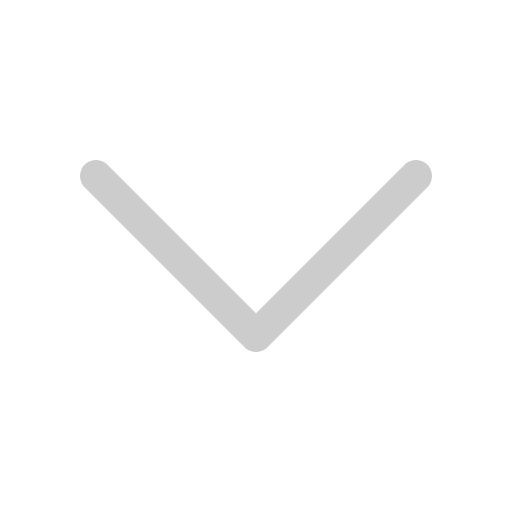
Do I need a stand or Filter Regulator Lubricator (FRL) with my filter crusher?
To use an oil filter crusher, you will need a stand and FRL if:
- your shop currently does not have a place to mount the crusher; and
- you do not have a proper air line with FRL in place.
Water in air lines is not a good thing for oil crushers or other air-operated equipment. We recommend a separate FRL for your oil filter crusher to maintain clean air and ensure the proper use of air pressure.
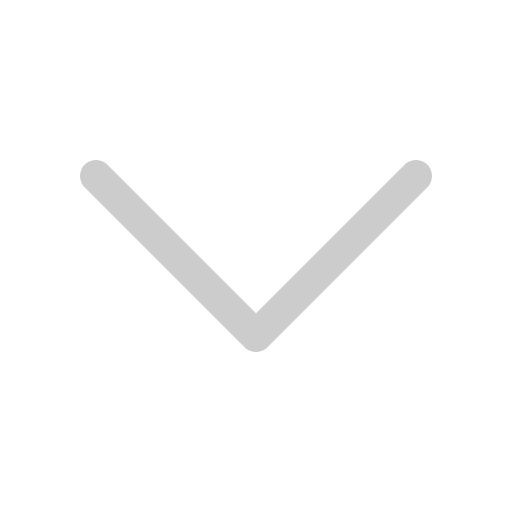
Do I need to crush my used oil filters before disposing of them?
Because of environmental regulations, most states require repair facilities to drain or remove more than 85% of used oil from a filter before disposal. If you hang filters upside down or stack them in a corner of your shop to let the oil drip off, the process could take all day or all night. Plus, you’re taking up valuable storage space, and you may not reach that 85% mark.
An oil filter crusher removes more than 95% of the residual oil from a filter. This is a much more efficient way to dispose of used oil filters because there’s no waiting for hours for the oil to drip off. Also, compressed filters take up less space. This faster process is safer for the environment and keeps you in compliance with regulations.
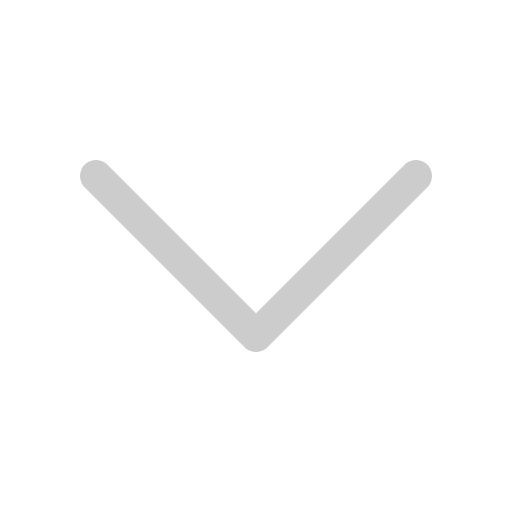
How do you crush a used oil filter?
First you need to get a filter crusher. These filter crushers remove more than 95% of the residual oil from the filter and make disposal much safer for the environment.
To crush a used oil filter, you simply place one filter in the crushing chamber with the open end of the filter facing downward within the area surrounded by the six centering posts. Then you close the door to activate the crushing cycle. When the unit stops running or runs noticeably slower, the crushing cycle is complete (NOTE: the crusher will not operate with the door open). Raise the door and carefully remove the crushed filter.
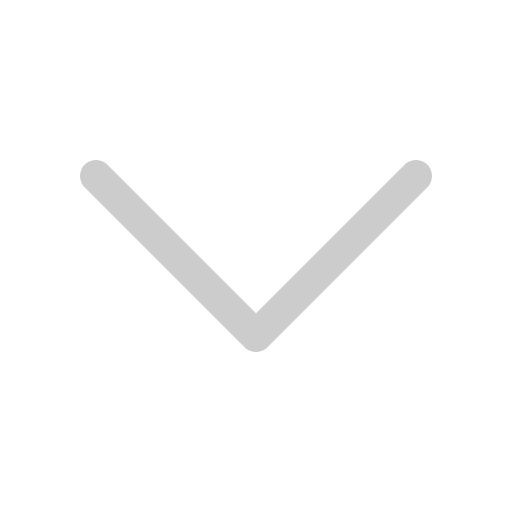
How fast does the fluid evacuator work?
The more viscous the fluid the faster it will take to evacuate. Warm oil or other fluid will flow faster than colder fluids. Also gear oil may take more time to evacuate than a traditional 10W30 weight oil.
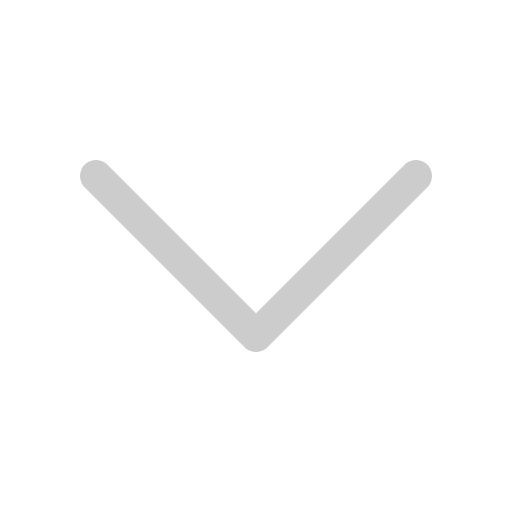
How do I know which probe to use with a fluid evacuator?
Unfortunately, there is no application data (year, make, and model of vehicle) for fluid evacuators, so you need to make sure you have the snuggest possible fit with the probe going into the dipstick. JohnDow Industries (JDI) Equipment’s fluid evacuators come with six probes that vary in width and length. Our steel fluid evacuators come with adapters for Mercedes, BMW, and Volkswagen.
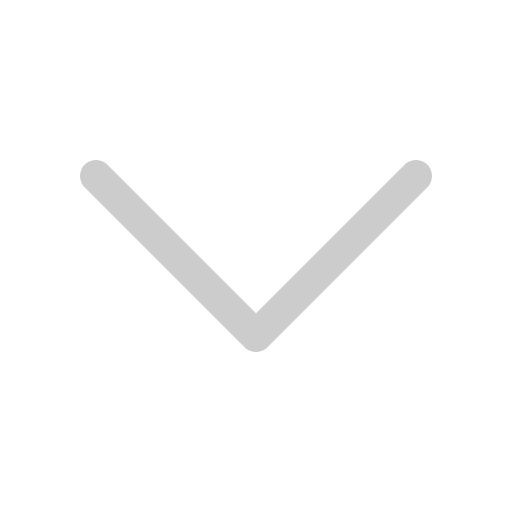
What type of fluid will the evacuators work with?
Any non-caustic or non-flammable fluids are ok to use with the fluid evacuators. The more viscous the fluid, the faster it will evacuate. Warm oil or other fluid will flow faster than cold fluids. Gear oil may take more time to evacuate than a traditional 10W30 weight oil.
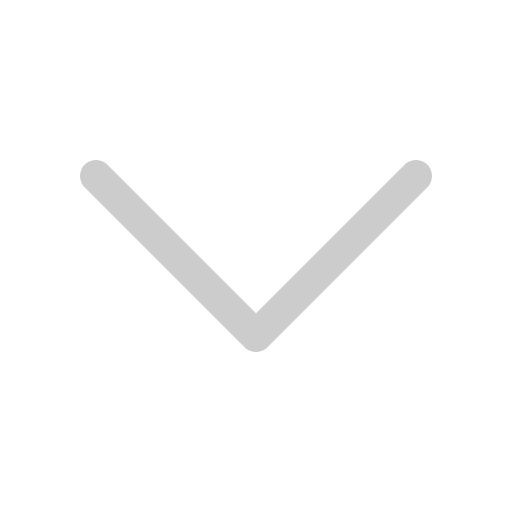
How does a fluid evacuator work?
Fluid evacuators remove used oil and other non-flammable fluids from almost any vehicle using compressed air and an on-board venturi vacuum system. They work best when the fluid is warmed up. To do this, idle the vehicle for a few minutes to get the fluids more viscous, then the evacuator will operate more efficiently.
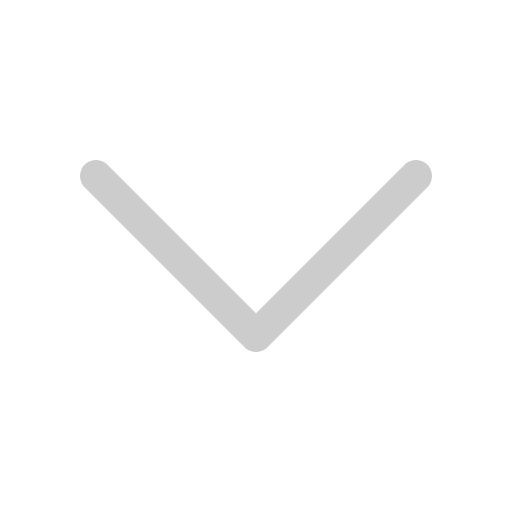
Do I need a fluid evacuator for my shop?
Shops who do oil changes or other fluid management work should have a fluid evacuator on site. If your shop works on import vehicles regularly, chances are at some point a vehicle will come in without a drain plug, where you’ll need to perform a fluid evacuation through the dip stick. Many import vehicles do not utilize drain plugs anymore. If you come across damaged or cross threaded drain plugs from a previous shops work, evacuating the oil will save you costly additional expenses like paying for an oil pan that was damaged by another shop.
Additionally, some vehicles have skid plates blocking the oil pan. Taking this skid plate off can take up significant time. Using a fluid evacuator from the dipstick virtually eliminates this method.
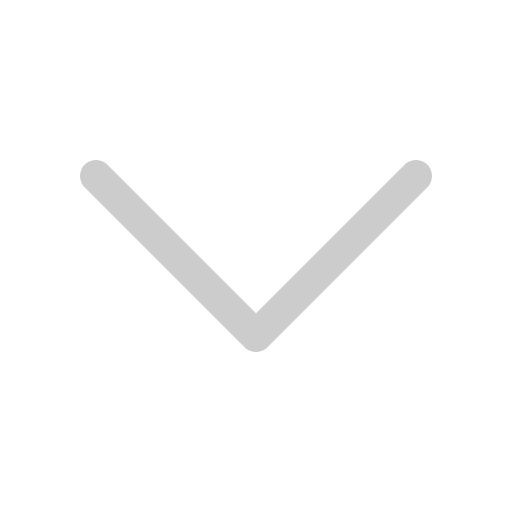
Why is my drain not emptying properly?
Most of the time, this happens when something falls into the downtube, like a nut or bolt. If this is not the issue, give us a call at 1-800-433-0708 to help you troubleshoot the issue.
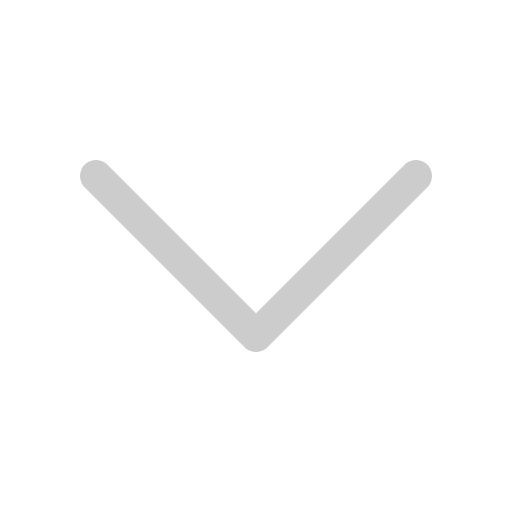
How much is an oil drain?
Oil drains vary in price depending on features, capacity and the type of material (usually plastic or steel). For an economy-style plastic drain (like our 8- or 18-gallon oil drains), you can expect to pay around $120 – $200. Larger capacity plastic drains can be as much as $700 in some cases. For steel self-evacuating drains (like our 18- to 25-gallon oil drains), you can expect to between $250 – $800 each.
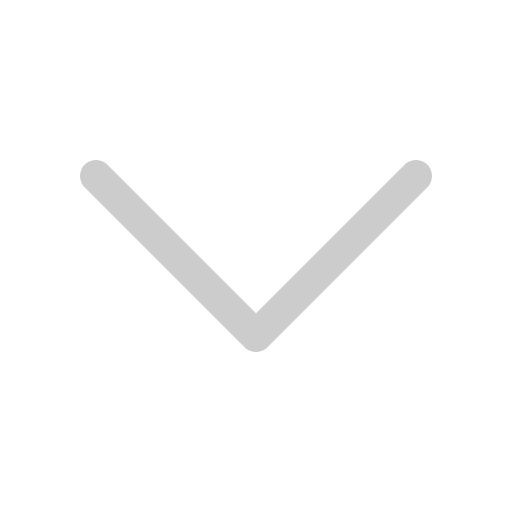
What is the right oil drain for my shop?
When you’re shopping for an oil drain, you should take a minute to ask yourself a few questions:
- How many oil changes are done in your shop daily? This will determine how big your oil drain needs to be.
- How do you store waste oil, and do you have a suction pump? This will lead you to the best oil drain style: self-evacuating or pump-assist.
- Do you work with expensive vehicles? This will help figure out whether to go with a poly or steel oil drain (You could damage cars with a steel version).
How big your oil drain needs to be
If oil changes are your main service, you need a large oil drain—possibly several of them. If your specialty is in another area, you can get by with a smaller oil drain.
Larger Oil Drains
You should invest in a large oil drain if changing oil is the main focus for your shop. A 25-gallon or 27-gallon oil drain would be ideal if you do a significant amount of oil changes on a typical day. You may even want to consider having multiple oil drains if oil changes are your primary service.
Smaller Oil Drains
You need to go with a small oil drain if your shop’s specialty is something besides oil changes (such as brakes and alignments). An 8-gallon or 18-gallon oil drain would be more suitable in this case. A small oil drain is a more affordable option for lower-volume repair shops, or even for DIYers at home.
The oil drain style you need
When determining whether you need a self-evacuating oil drain or a pump-assist oil drain, consider the following:
Self-evacuating oil drains use shop air to empty used oil and get the equipment back to the service floor. Capacities include 18, 25, and 27 gallons. An 18-gallon oil drain works well for shops who don’t do a ton of oil changes and have fewer bays, where shops who have an oil change focus with multiple bays would need drains that hold 25 or 27 gallons of oil. No auxiliary equipment—such as a diaphragm pump—is needed, so the initial investment of a self-evacuating oil drain is lower because you don’t have to add the expense of a diaphragm pump.
A pump-assist oil drain lets you hook up a suction hose directly to a full oil drain and transfer oil from the drain to the waste oil tank. Shop air usually runs the suction pump. Pump-assist oil drains can vary in size from 8 gallons for a smaller shop with a couple of bays to around 30 gallons for a high-volume operation with multiple bays. Shops already using a diaphragm pump can benefit the most from using a pump-assist oil drain to empty used oil, and then get back to work quickly.
Determining if you need a steel or poly oil drain
Steel oil drains hold up well and can last a long time. But if you’re working on higher-end or specialty vehicles, you may want to consider a poly oil drain. If a technician bumps an expensive car with a steel oil drain, there could be damage left behind.
Our steel oil drains come in the following sizes: 16, 17, 18, 22, and 25 gallons.
If you are a lower-volume repair shop or a DIYer, an 8- or 18-gallon poly oil drain would be more suitable for your operation. If you are a bigger operation and want a poly oil drain, we offer them in the following additional sizes: 17, 22, and 27 gallons.
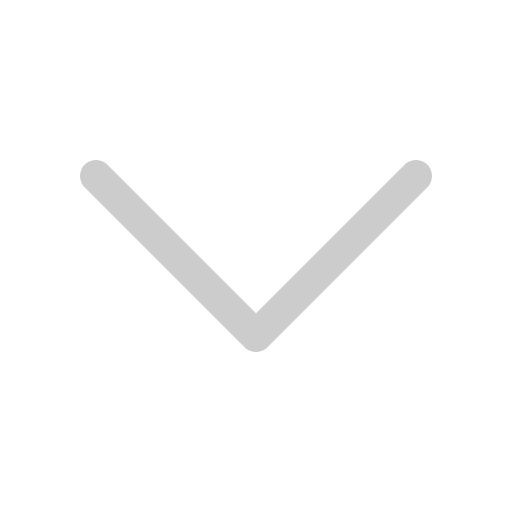
What is a pump-assist oil drain?
A pump-assist oil drain lets you hook up a suction hose directly to a full oil drain and transfer oil from the drain to the waste oil tank. Shop air usually runs the diaphragm suction pump.
Pump-assist oil drains can vary in size from 8 gallons for a smaller shop with a couple of bays to around 30 gallons for a high-volume operation with multiple bays. Shops already using a diaphragm pump can benefit the most from using a pump-assist oil drain to empty used oil, and then get back to work quickly.
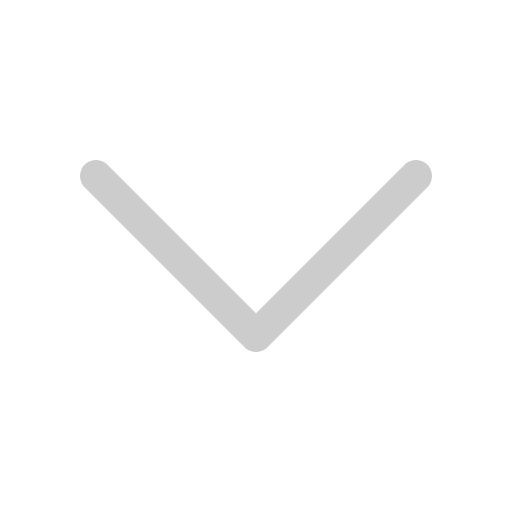
What is a self-evacuating oil drain?
Self-evacuating oil drains use shop air to empty used oil and get the equipment back to the service floor. Capacities include 18, 25, and 27 gallons. An 18-gallon oil drain works well for shops that don’t do a ton of oil changes and have fewer bays; whereas, shops that have an oil change focus with multiple bays would need drains that hold 25 or 27 gallons of oil.
With self-evacuating oil drains, no auxiliary equipment—such as a diaphragm pump—is needed. So, the initial investment of a self-evacuating oil drain is lower because you don’t have to add the expense of a diaphragm pump.
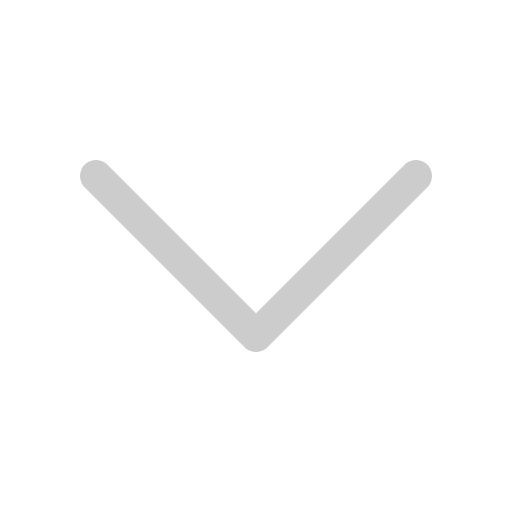
What is “auto check technology”?
JDI’s Auto-Check Technology is exclusive to our self-evacuating oil drains. It utilizes a check ball in the bottom of the downtube to automatically seat up when shop air is hooked up to the drain. No one else’s drains work this way.
Auto-Check Technology eliminates the need for a large ball valve in the downtube. It also makes emptying the drain much easier for the shop technician. There’s no need to remember to close the ball valve when hooking up shop air. This avoids oil geysers that most shops have experienced at one time or another when using other self-evacuating oil drains.
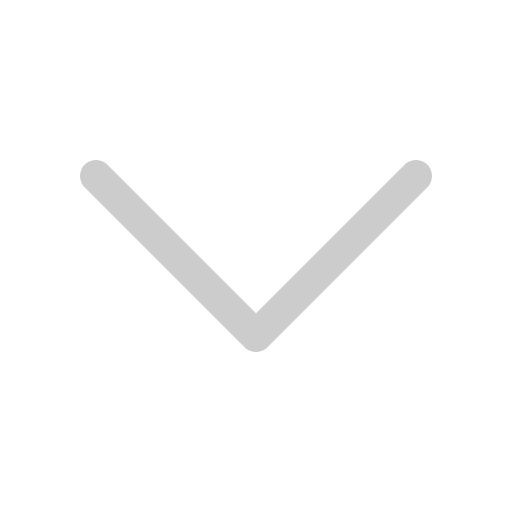
How Do I Choose Between Steel or Poly Oil Drains?
Steel oil drains hold up well and can last a long time. But if you’re working on higher-end or specialty vehicles, you may want to consider a poly oil drain. If a technician bumps an expensive car with a steel oil drain, there could be damage left behind.
Our steel oil drains come in the following sizes: 16, 17, 18, 22, and 25 gallons.
If you are a lower-volume repair shop or a DIYer, an 8- or 18-gallon poly oil drain would be more suitable for your operation. If you are a bigger operation and want a poly oil drain, we offer them in the following additional sizes: 17, 22, and 27 gallons.
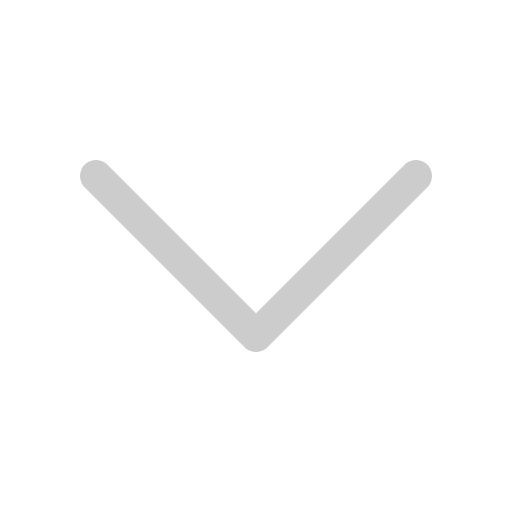
How do I determine the size oil drain I need?
It depends. You’ll need to make your decision based on the way your business operates.
If oil changes are your main service, you need a large oil drain (20 gallons or more)—possibly several of them. If your specialty is in another area, you can get by with a smaller, 8- or 18-gallon oil drain.
Larger Oil Drains
You should invest in a large oil drain if changing oil is the main focus for your shop. A 25-gallon or 27-gallon oil drain would be ideal if you do a significant amount of oil changes on a typical day. You may even want to consider having multiple oil drains if oil changes are your primary service.
Smaller Oil Drains
You need to go with a small oil drain if your shop’s specialty is something besides oil changes (such as brakes and alignments). An 8-gallon or 18-gallon oil drain would be more suitable in this case. A small oil drain is a more affordable option for lower-volume repair shops, or even for DIYers at home.
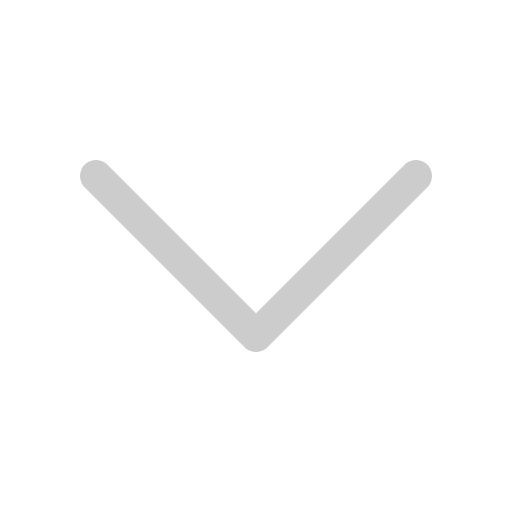
Are your HVLS fans made in the USA?
Yes, our HVLS fans are made and assembled in the USA.
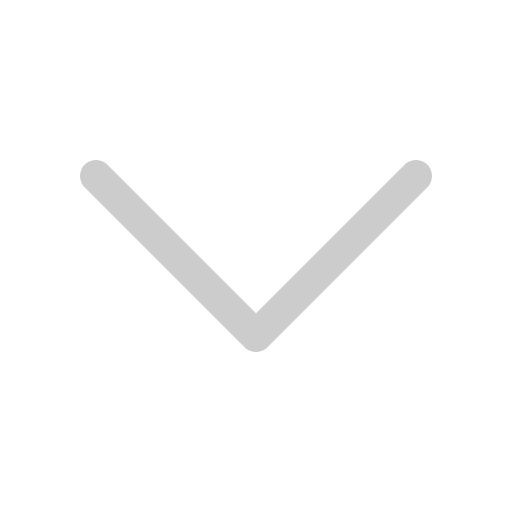
How much do HVLS fans cost?
HVLS fans vary in size, number of blades, and blade colors. Because of these variables along with your facility layout, cost differs for each project. Please contact us so we can help you with a quote.
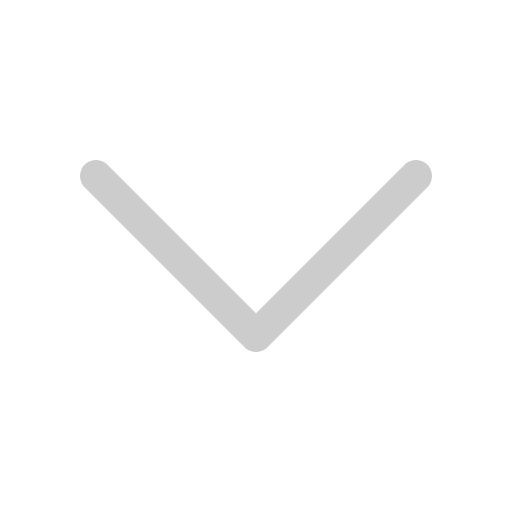
Do you have a warranty on your products?
Yes! EuroVent HVLS fans carry a warranty of five (5) years on all parts and components. The warranty period begins on date of shipment. The installation manual outlines complete warranty coverage information.
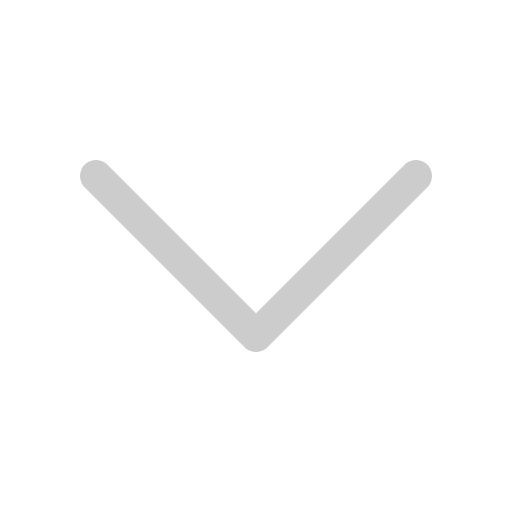
I have a technical question. Who can I talk to?
Give us a call at 1.888.433.0708 or fill out this form. We have experts with over 18 years of experience to help you with any question you may have.
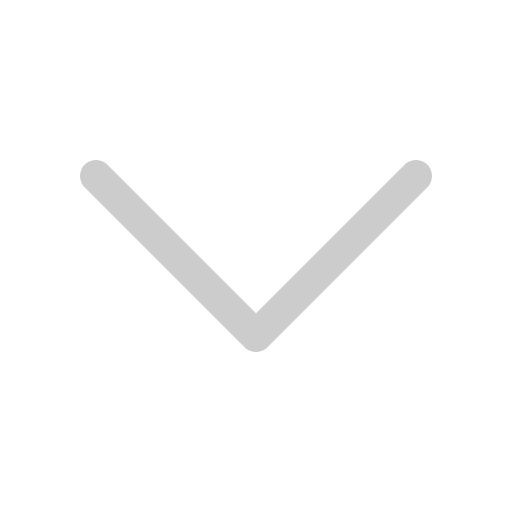
How do I get replacement parts?
Please contact us if you are having any issues with your EuroVent HVLS fan. We can help coordinate replacement parts for your system, if needed.
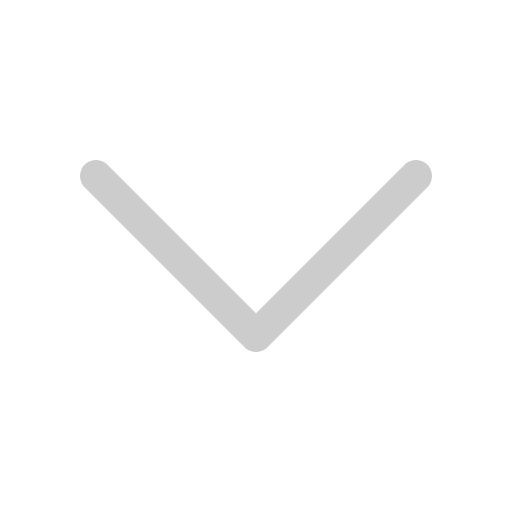
How do I find a distributor?
If you are looking for a EuroVent Exhaust Extraction System or HVLS fan distributor, please fill out this form and we will contact you with a distributor in your area that would fit your needs.
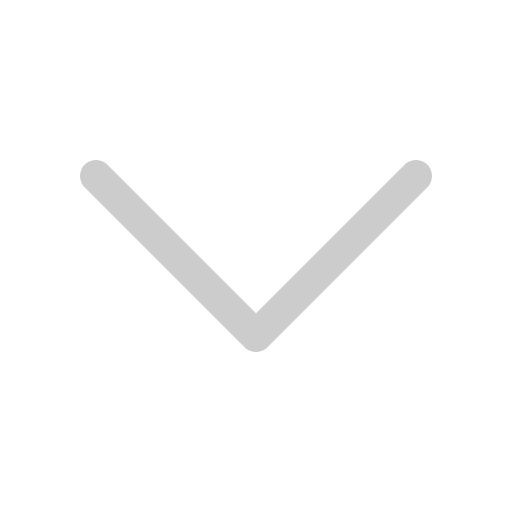
Do you sell direct?
No. We sell through equipment distributors across the country because of their expertise and project installation. Please contact us and we can provide you with a local distributor specific to your project.
All orders must take place through an authorized EuroVent distributor or sales representative.
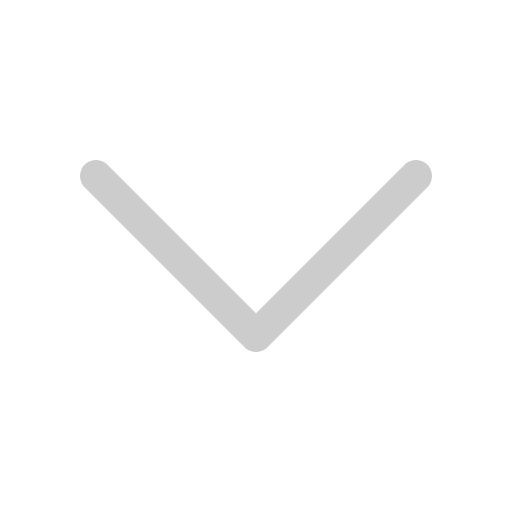
How are HVLS fans controlled?
EuroVent HVLS fans feature a Keypad control, which can operate with 1,3,5, or 10 fans.
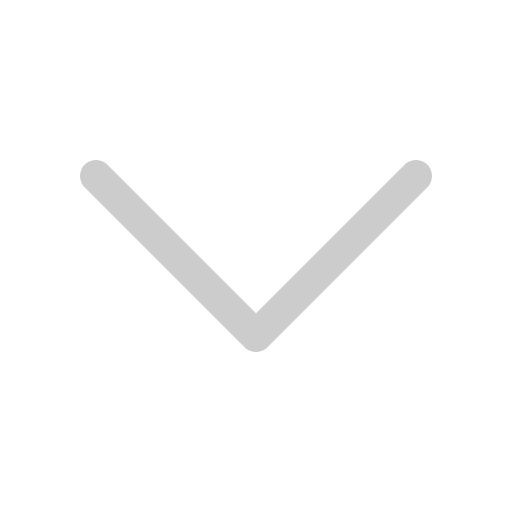
How many HVLS fans do I need?
This depends on you’re the size of your facility size, ceiling height, desired area and size of fan. To get a better understanding of what is best for you, please reach out to us.
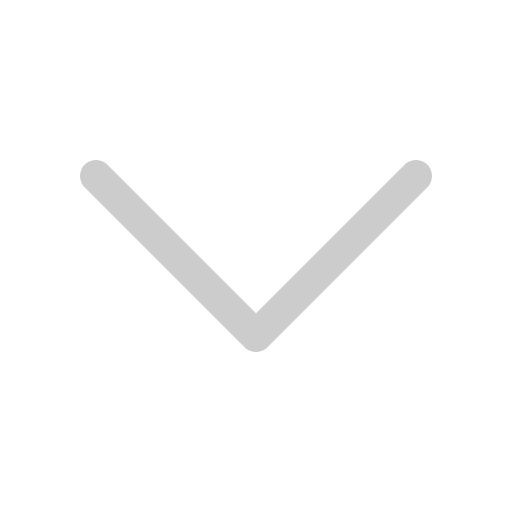
How much area does an HVLS fan cover?
EuroVent HVLS fans cover as low as 9,200 square feet with an 8-foot diameter 5-blade HVLS fan, up to 18,700 square feet with a 24-foot diameter 3-blade HVLS fan.
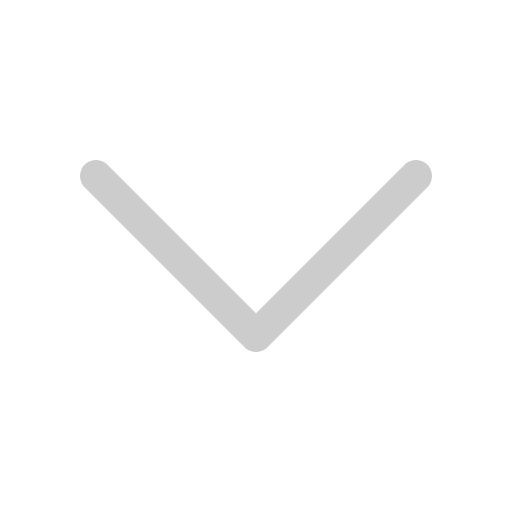
How is HVLS performance measured and what should I look for?
Not all HVLS fans are created equal and are not the same. When it comes to performance, look for:
- Maximum Cubic Feet per Minute (CFM)
- Efficiency Cubic Feet per Minute per Watt (CFM/W)
- coverage area in square feet
- dBA at Maximum RPM (needs to be less than 85 dBA; the rate at which long or repeated exposure to sound can cause hearing loss)
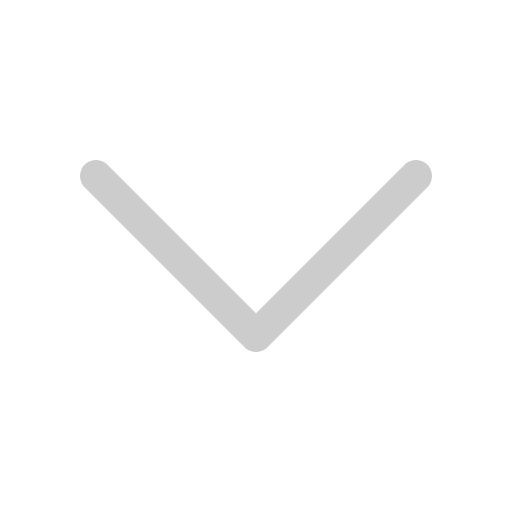
Can HVLS fans come in different colors?
Yes with an additional charge. EuroVent’s HVLS fan blades come standard with a brushed aluminum finish. If you wanted a specific color, we do offer custom color match for an additional charge.
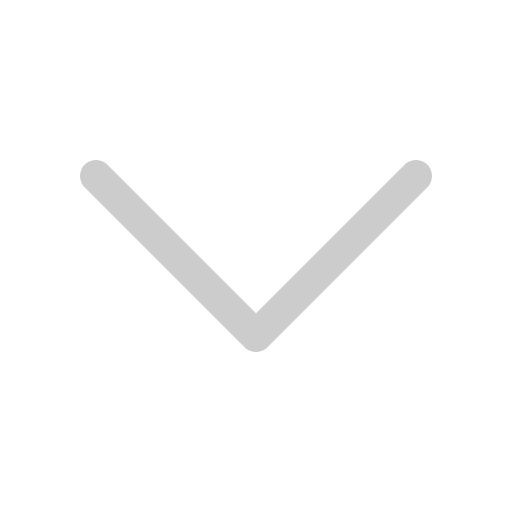
Is there a difference between a 3-blade and 5-blade HVLS fan?
Yes. More blades does not necessarily mean better performance. EuroVent’s 5-blade fan is ideal for small spaces with low- or medium-height ceilings, where EuroVent’s 3-blade fan is ideal for medium to large spaces with medium- to high-height ceilings.
EuroVent’s 5-blade HVLS fan has diameter options of 8’, 10’, 12’ or 14’ and creates air movement coverage up to 54,900 cubic feet per minute.
EuroVent’s 5-blade HVLS fan has diameter options of 16’, 18’, 20’ or 24’ and creates air movement coverage up to 164,900 cubic feet per minute.
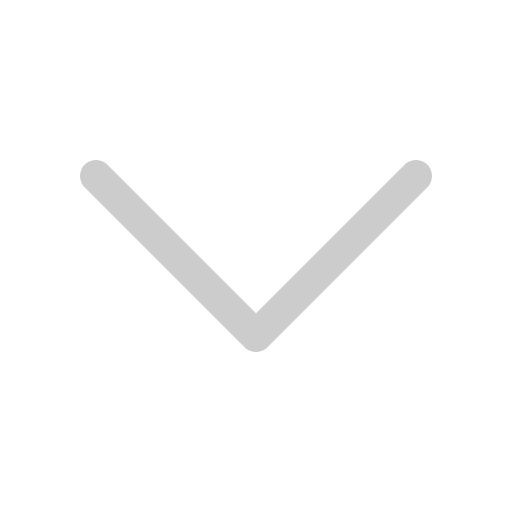
What other ceiling fan requirements are there?
In addition to DOE Efficiency legislation, HVLS fans must be in accordance to Fire code – nfpa 13. This code includes:
- Maximum fan diameter shall be 24 ft.
- Fan shall be centered between 4 sprinklers
- Vertical clearance to sprinkler deflector shall be minimum of 3 ft.
- Fans shall be interlocked to shut down upon receiving fire alarms
HVLS fans must also me in accordance of ASHRAE 55 – Comfort Cooling. ASHRAE 55 establishes methodology for quantifying the effect of air velocity on thermal comfort
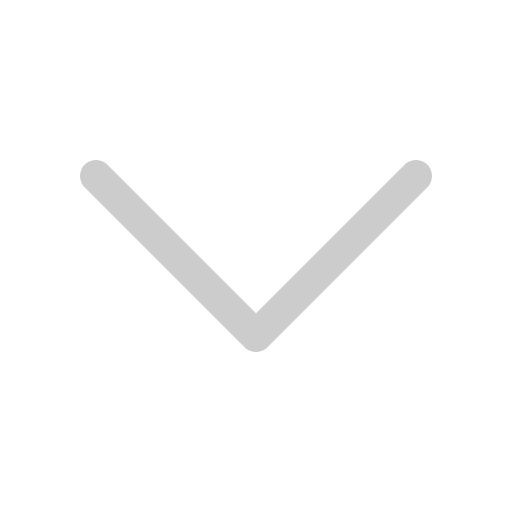
What is a direct drive fan? What is a conventional (or gearbox-driven) motor? And what is the difference?
A direct drive fan is a smaller, quieter, more efficient motor compared to a gearbox-driven motor. With a gearbox-driven fan, the motor provides powers the gearbox, which in turn powers the blades to turn. A direct drive uses a motor to power the blades, eliminating the need and issues related to a gearbox.
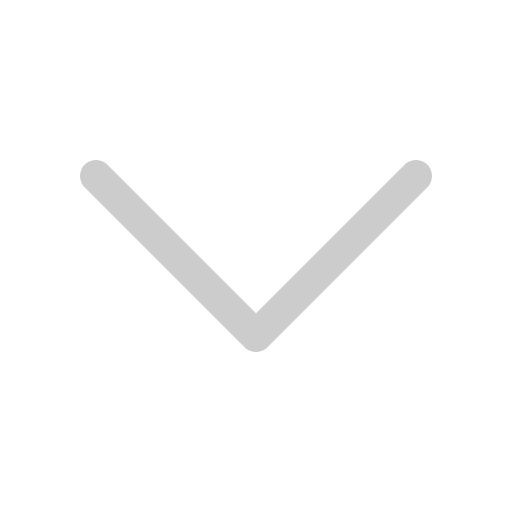
Are there efficiency standards for ceiling fans?
Yes. The Department of Energy (DOE) sets standards for efficiency in ceiling fans by measuring cubif feet per minute per watt (CFM/W) used to power the fan.
All EuroVent HVLS fans cover nearly twice the DOE’s minimum standard of CF/W.
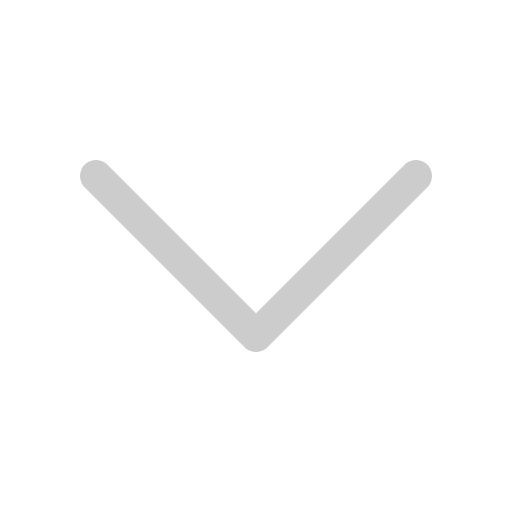
How do HVLS fans save energy?
Using low speeds, HVLS fans use a fraction of the energy of conventional fans while providing a comfortable indoor breeze. The 3-5 mph breeze generated by a EuroVent HVLS fan creates a cooling sensation by as much as 10°F, supplementing air conditioning systems for a higher thermostat setting.
With destratification, an HVLS fan creates a more uniform and comfortable temperature, further allowing thermostat settings to maintain for longer periods of time.
Direct drive motors in HVLS fans use 20% less energy than gearbox-driven motors.
EuroVent HVLS fans generate up to 30 percent more airflow and only need half the amount of horsepower compared to other HVLS fans.
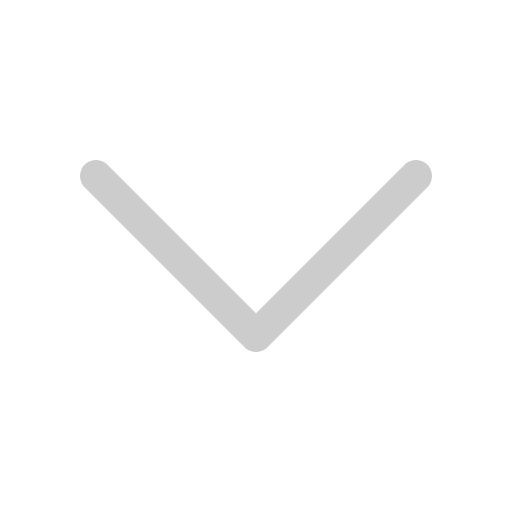
What is destratification?
Destratification is the process of mixing the rising warmer air trapped at the ceiling with the colder air at the floor level. This creates a more uniform and comfortable temperature from floor to ceiling. It also allows for thermostat settings to maintain for longer periods of time to reduce energy costs.
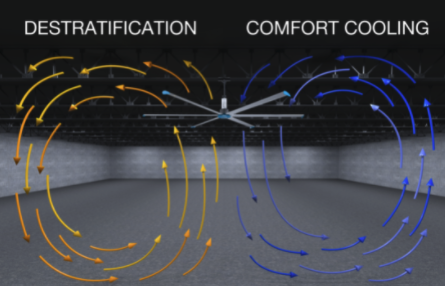
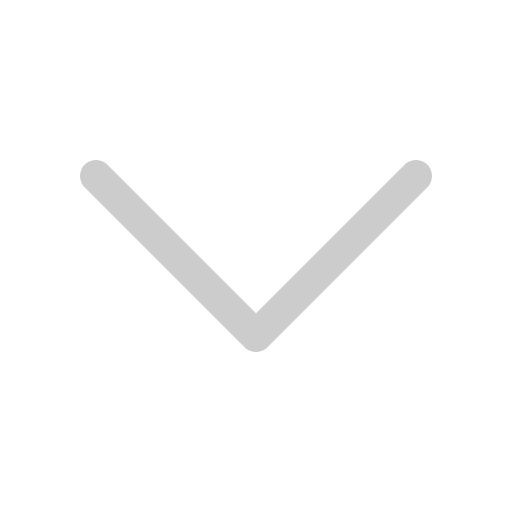
How fast are HVLS fans?
EuroVent HVLS fans generally range in speed of 3-5 mph.
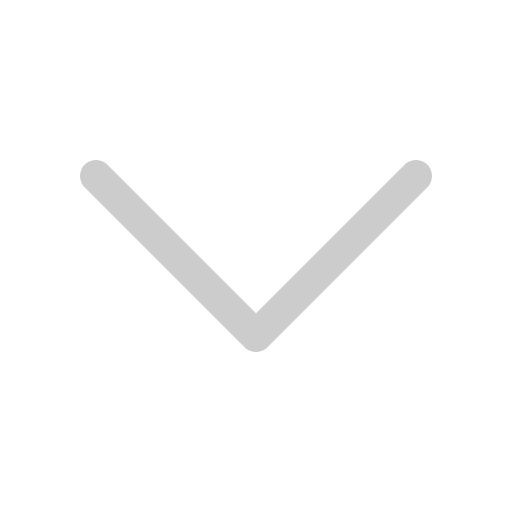
How big are HVLS fans?
EuroVent HVLS fans can range in size from 8 feet up to 24 feet in diameter.
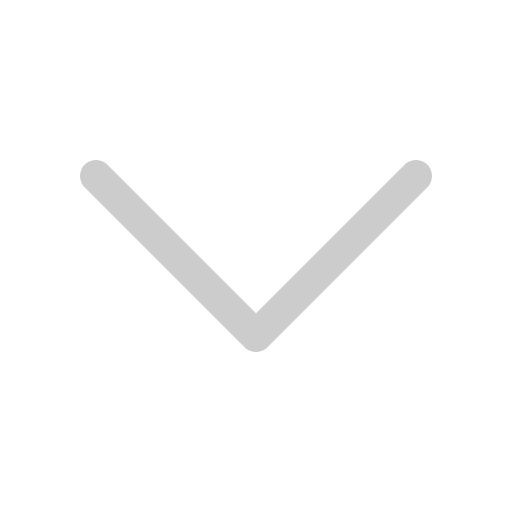
Why would I need an HVLS fan?
It is always wise to have great air circulation, especially when operating a larger facility. Facilities that benefit from HVLS fans the most are:
– Office spaces – Restaurants and bars – Education facilities – Supermarkets – Retail stores – Fitness centers | – Airports – Gyms – Agricultural facilities – Manufacturing facilities – Automotive facilities – Distribution Centers – Stadiums & Arenas |
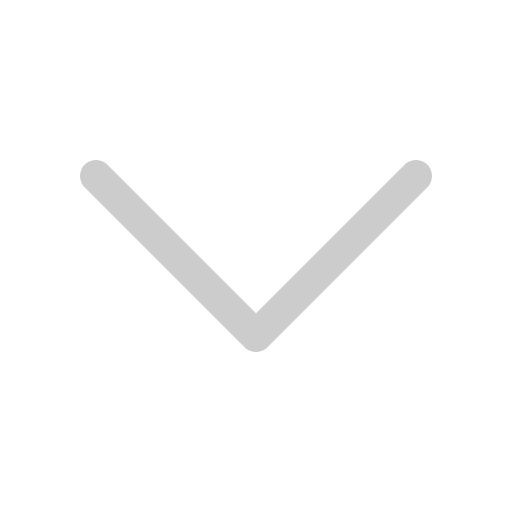
What is an HVLS Fan?
An HVLS fan, or High-Volume Low-Speed fan is a larger ceiling fan that moves at a slow speed while circulating a large amount of air.
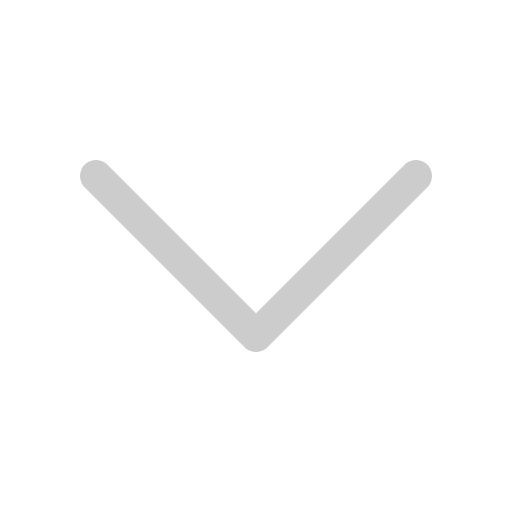
I have a product development idea. Who can I talk to?
Give us a call at 1-800-433-0708 or fill out this form.
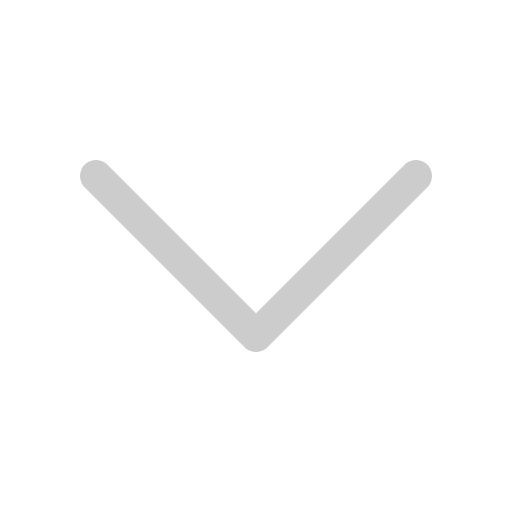
Do you have a warranty on your products?
Yes, however they vary depending on your product. Generally speaking:
Service Equipment:
JohnDow Service Equipment products which prove to be defective in material and workmanship within one (1) year from the date of purchase may be returned freight prepaid for repair, replacement or credit at the discretion of JohnDow personnel. If JohnDow inspection discloses no defect in material or workmanship, repair, replacement or return will be made at customary charges. This warranty does not cover failure of parts or components due to normal wear or damage, wear which in the judgment of JohnDow arose from misuse, abrasion, negligence, accident, faulty installation, or tampering.
Dynamic Back Shop Supplies and TPMS:
JohnDow Dynamic back shop supply and TPMS products which prove to be defective in material and workmanship within one (1) year from the date of purchase may be returned freight prepaid for repair, replacement or credit at the discretion of JohnDow personnel. If JohnDow inspection discloses no defect in material or workmanship, repair, replacement or return will be made at customary charges This warranty does not cover failure of parts or components due to normal wear or damage, wear which in the judgment of JohnDow arose from misuse, abrasion, negligence, accident, faulty installation, or tampering.
EuroVent:
EuroVent exhaust extraction products (except aluminum rail and neoprene seal) which prove to be defective in material and workmanship within one (1) year from the date of purchase are returnable with freight prepaid for repair, replacement or credit. If the fan and/or motor was not installed per the manufacturer’s drawing, the fan and/or motor warranty may be void.
Limited Lifetime Warranty – Aluminum Rail & Neoprene Seal
JohnDow warrants the rail and neoprene seal is free from defects in materials and manufacture for as long as the original purchaser owns the system. The warranty does not include normal wear and tear or failure to misuse, carelessness or any accidental cause.
HVLS Fans
EuroVent HVLS fans carry a warranty of five (5) years on all parts and components. The warranty period begins on date of shipment. The installation manual outlines complete warranty coverage information.
If you have a question about a specific product, please reach out to us by calling 1-800-433-0708 or fill out this form.
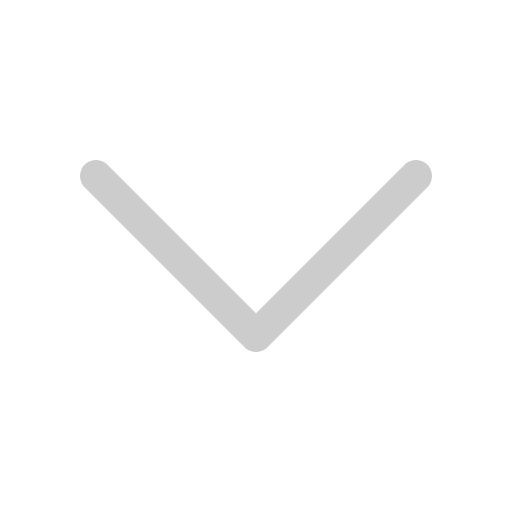
How can I purchase your products?
We work with a variety of distributors throughout the United States who sell our service equipment, both in person and online. If you already have a preferred repair facility equipment distributor, we suggest starting with them to find the equipment you’re looking to purchase. If you don’t have a preferred distributor, fill out this form and we will connect you with the right fit.
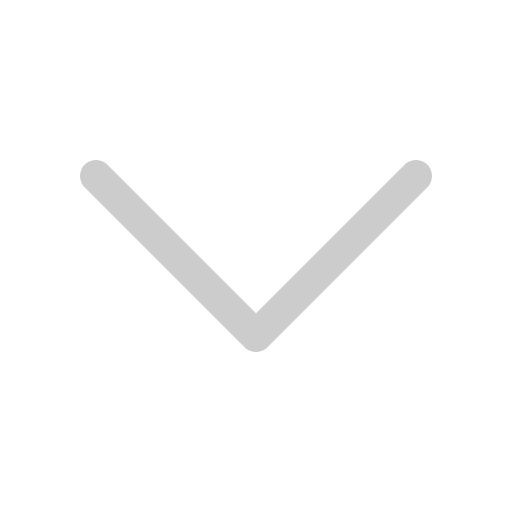
How can I reach you?
Still have a question? Email us at CustomerService@JohnDow.com, call us at 1-800-433-0708, or fill out this form.
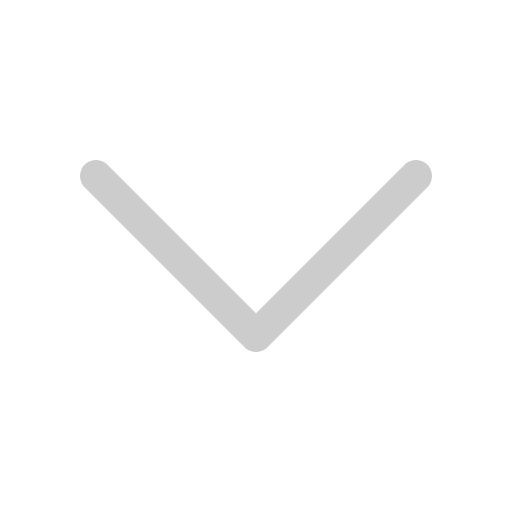
Are products made in the USA?
We source materials from across the world, where many of our products are made and assembled right here in the USA.
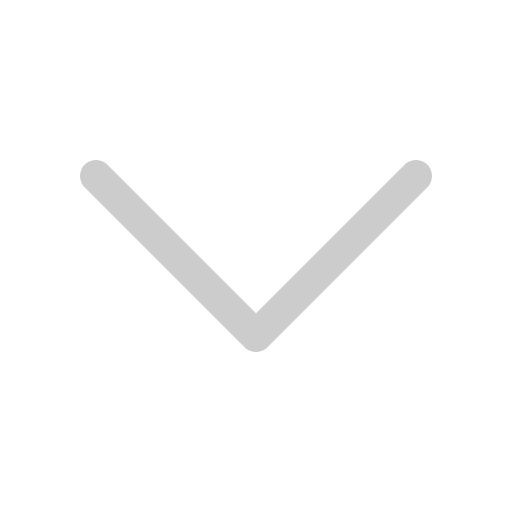
Are your products available internationally?
All JohnDow products are available in the US and Canada.
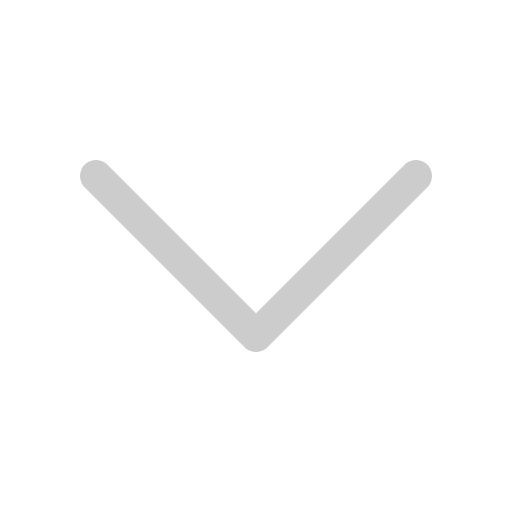
Where do you ship from?
We ship all of our products from our Barberton, Ohio facility, zip code 44203.
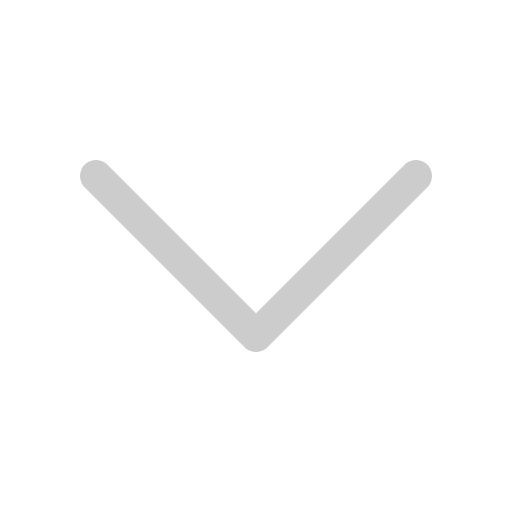
Do you have a warranty on your products?
Yes, JohnDow Service Equipment products which prove to be defective in material and workmanship within one (1) year from the date of purchase may be returned freight prepaid for repair, replacement or credit at the discretion of JohnDow personnel. If JohnDow inspection discloses no defect in material or workmanship, repair, replacement or return will be made at customary charges. This warranty does not cover failure of parts or components due to normal wear or damage, wear which in the judgment of JohnDow arose from misuse, abrasion, negligence, accident, faulty installation, or tampering.If you have a question about a specific product, please reach out to us by calling 1-800-433-0708 or fill out this form.
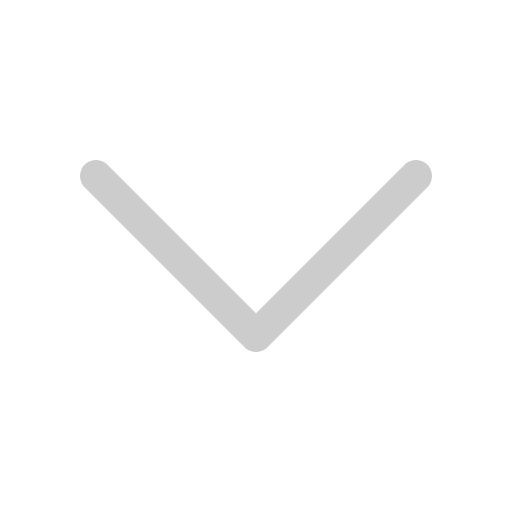
I have a technical question. Who can I talk to?
The experts on our technical team is well-versed in all of our products. If you have a technical question, you can email us at CustomerService@JohnDow.com, call us at 1-800-433-0708, or fill out this form.
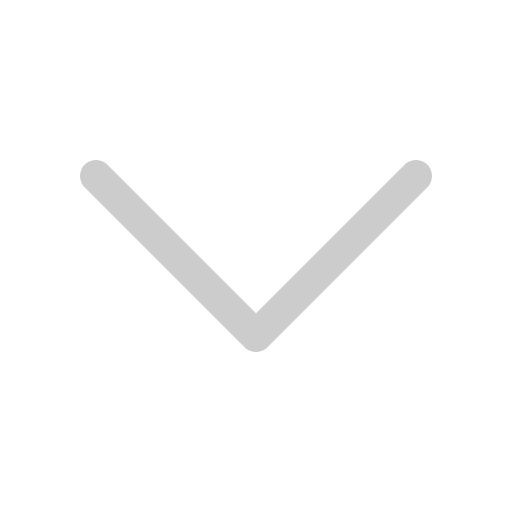
Something may be wrong with fuel caddy. What do I do?
If something is wrong with your fuel caddy, please email us at CustomerService@JohnDow.com, call us at 1-800-433-0708, or fill out this form.
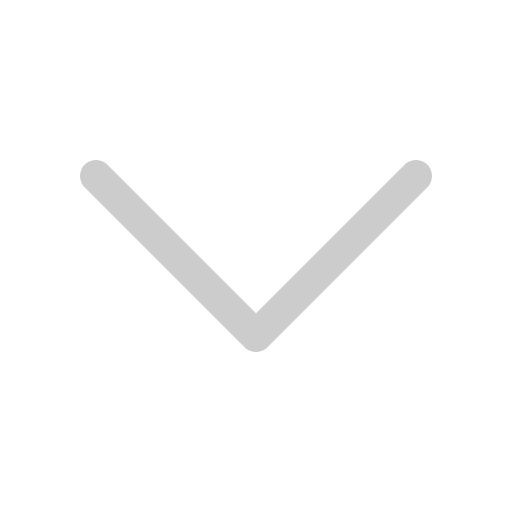
How do I get replacement parts?
If you need replacement parts for any JohnDow product, please email us at CustomerService@JohnDow.com, call us at 1-800-433-0708, or fill out this form.
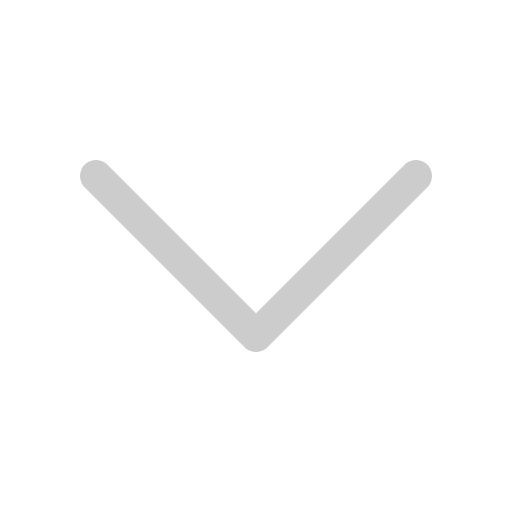
Are your instructions or user manuals online?
For most of our products, yes. You can find instructions, or the User Manual, at the bottom of each product’s page. Included are any relevant documents under Resource Downloads.
Some products require professional installation and expertise, where those instructions are provided at the time of service.
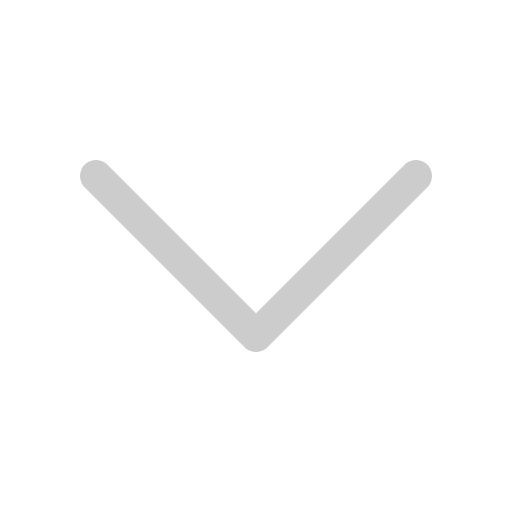
Can I put gasoline in the Diesel Carrytanks?
No. The Diesel Carrytanks are not approved or rated for gasoline. Using gasoline in a Diesel Carrytank will create a fire risk.
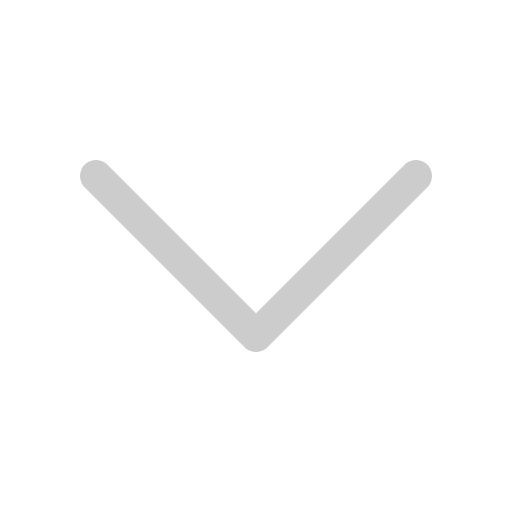
Do you carry gas or diesel caddies for commercial or heavy-duty vehicles?
If you need to transport a large amount of diesel, we offer diesel Carrytanks in two sizes, 58 gallons and 106 gallons. The 106-gallon Diesel Carrytank is designed to fit a 10-gallon Diesel Exhaust Fluid (DEF) tank, if needed.
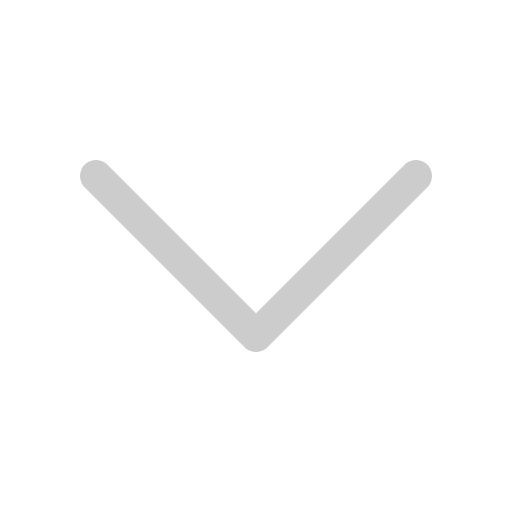
How do I find a distributor?
If you already have a preferred distributor, we suggest starting with them to find what you’re looking to purchase. If you don’t have a preferred distributor, fill out this form and we will connect you with the right fit.
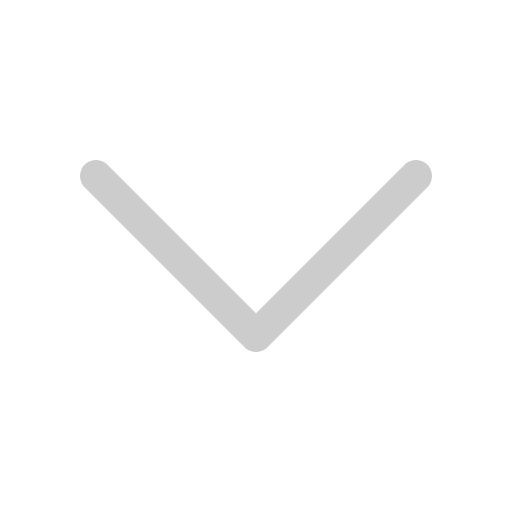
Where can I purchase a fuel caddy?
We work with a variety of distributors throughout the United States who sell our service equipment, both in person and online. If you already have a preferred tool and equipment distributor, we suggest starting with them to find the equipment you’re looking to purchase. If you don’t have a preferred distributor, fill out this form and we will connect you with the right fit.
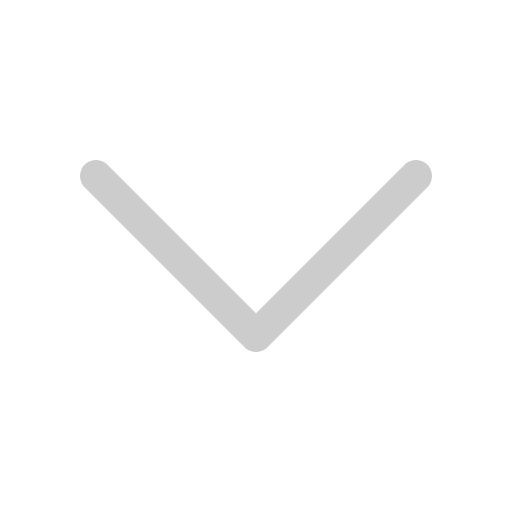
Do you sell direct?
We do not sell direct, however you can find all of our product offerings through popular tool and equipment distributors. If you already have a preferred repair facility equipment distributor, we suggest starting with them to find the equipment you’re looking to purchase. If you don’t have a preferred distributor, fill out this form and we will connect you with the right fit.
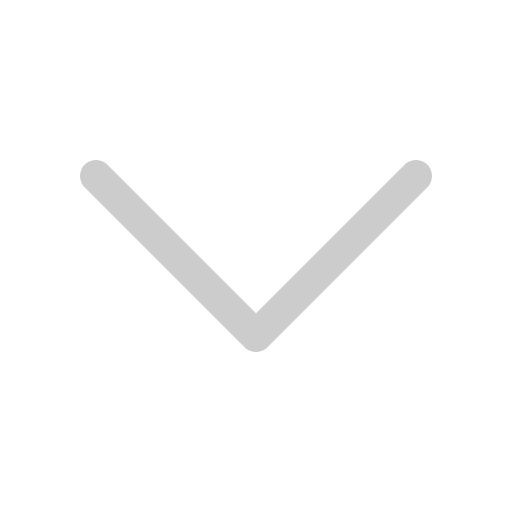
Can I alter a fuel caddy?
No. You should never alter a fuel caddy other than adding an approved fuel pump. Altering a gas caddy will void any warranty and governing body approval (UL Listed and UN/DOT approval).
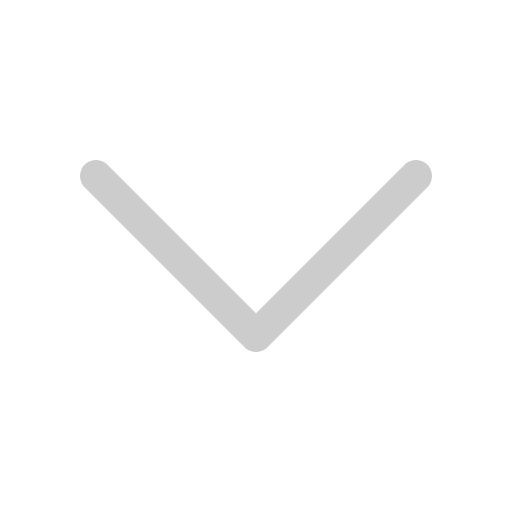
Can I get a pump for a fuel caddy?
Yes. We offer rotary hand pumps and pump kits for steel and poly fuel caddies.
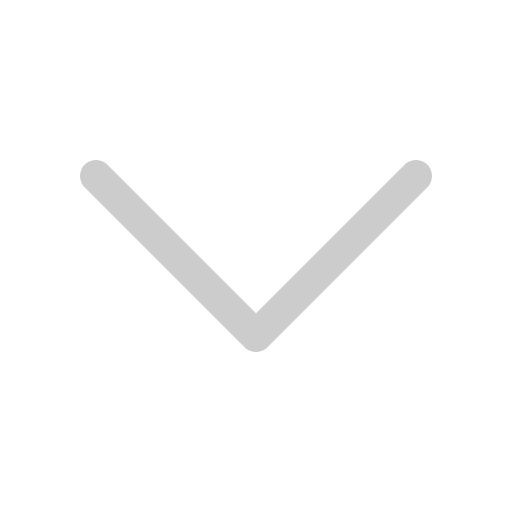
How does the fuel in a poly fuel caddy flow?
A poly fuel caddy uses gravity to dispense the fuel from the caddy to the tank you are filling. In most cases, you can purchase an optional rotary pump kit to empty the fuel from the caddy to the tank you are filling.
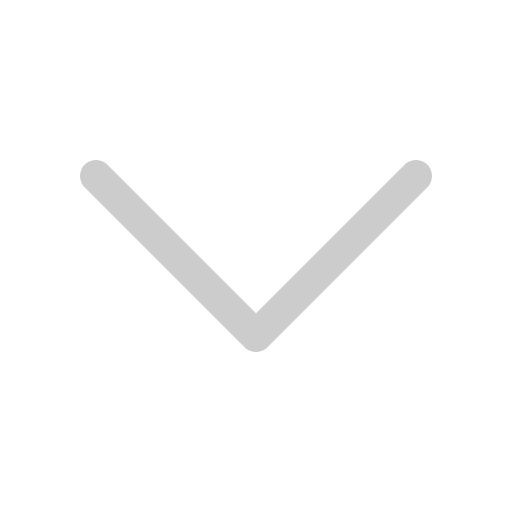
How big are fuel caddies?
Our steel fuel caddies come in two sizes. We offer 25-gallon and 30-gallon fuel caddies for both gasoline and diesel.
Our poly fuel caddies also come in two sizes. We offer 15- and 25-gallon gasoline caddies in red, and a 25-gallon diesel caddy in yellow.
If you need to transport a large amount of diesel, we offer diesel Carrytanks in two sizes, 58 gallons and 106 gallons.
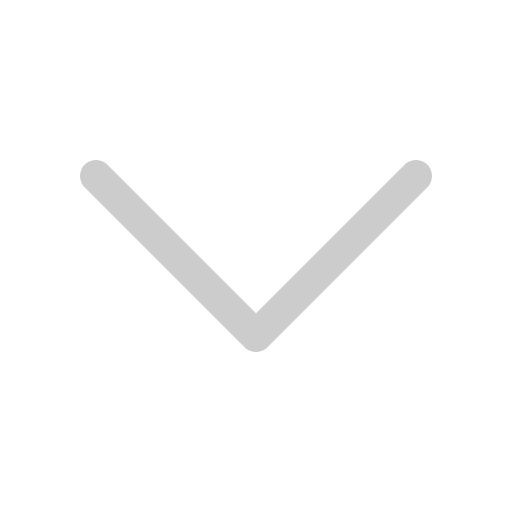
Do I need a plastic or steel fuel caddy?
If you are temporarily storing fuel to be put back in a vehicle, a U.L. listed steel caddy is the way to go. If you are transporting fuel over the road, a UN/DOT approved plastic fuel caddy is what you will need.
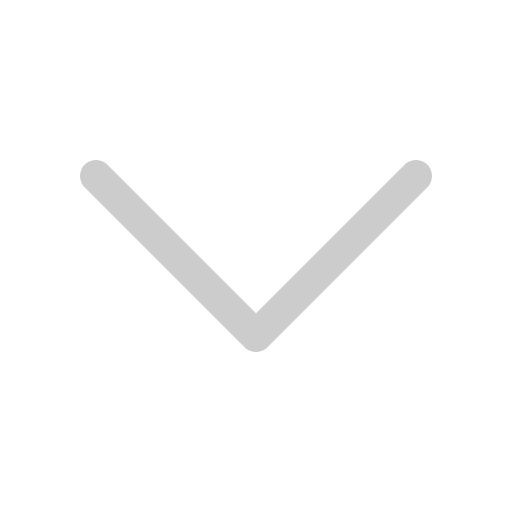
Can I put gas in my diesel caddy or vice versa?
To avoid mixing and contamination, a caddy needs to be dedicated to a specific type of fuel. Any container used to store gas or diesel must be properly marked with the stored fuel. Generally, gas is kept in a red caddy, and diesel is stored in a yellow caddy. This allows technicians to easily identify each fluid in the shop.
Simply put, you should not put gas in a diesel caddy because you’d create a safety hazard. Improper storage of flammable and combustible liquids such as diesel and gas can lead to fires or explosions. Storing gas in a gas-designated caddy that is U.L. listed and meets Occupational Safety and Health Administration (OSHA) standards is the best way to ensure safety.
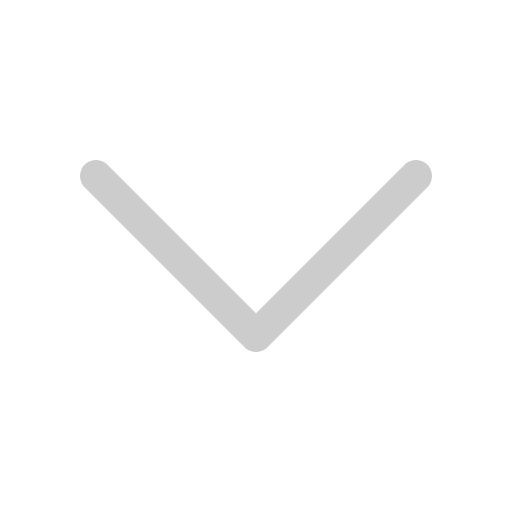
What is the difference between a gas caddy and a diesel caddy?
If your shop deals with gasoline and diesel, you must have the appropriate containers. You cannot store gasoline in a diesel caddy or vice versa. To avoid mixing and contamination, you need to dedicate each caddy to a specific type of fuel. Generally red fuel caddies are designated for gasoline, and yellow fuel caddies are designated for diesel. This allows technicians to easily identify each fluid in the shop and not waste time trying to figure out which is gasoline and which is diesel.
Improper storage of flammable and combustible liquids can lead to serious fires or explosions. You must properly mark the type of stored fuel on any container used to store gasoline or diesel.
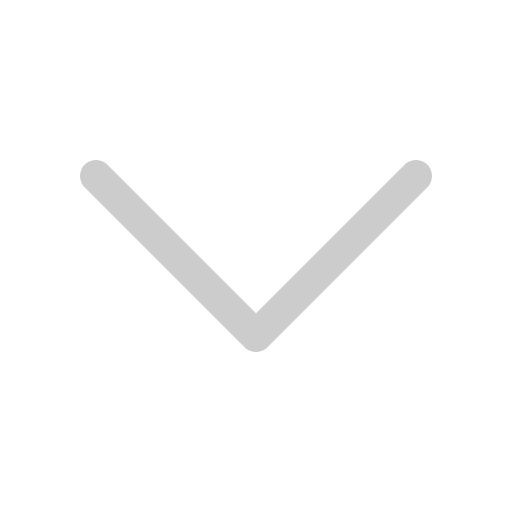
What’s the major difference between U.L. Listed fuel caddies and UN/DOT approved fuel caddies?
If the need is to temporarily store fuel like in a shop setting, like when replacing a fuel pump, you’ll need a U.L. listed fuel caddy. If the need is to transport fuel over the road, like going on a weekend ATV trip, you’ll need a UN/DOT container.
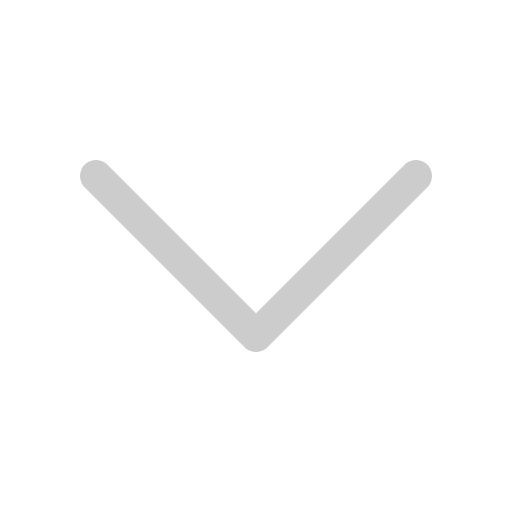
What kinds of fuel caddies are available?
There are two main types of fuel containers: U.L. listed steel fuel caddies and UN/DOT-approved poly fuel caddies. U.L. listed steel fuel caddies provide temporarily fuel storage in a professional repair facility. UN/DOT-approved poly fuel caddies are for transporting fuel on public roads.
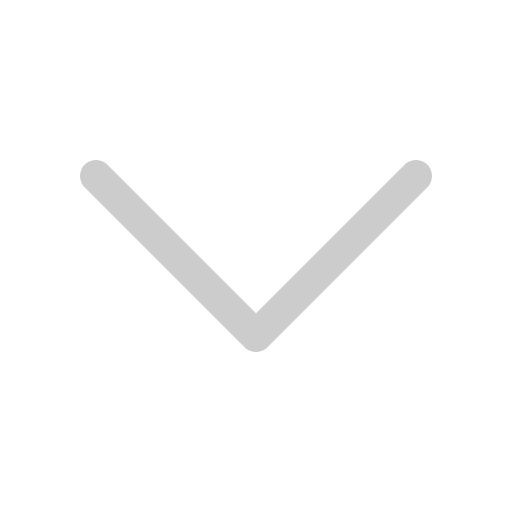
Do I need a UL Listed fuel caddy?
You need a U.L. listed steel fuel caddy when you’re going to temporarily store fuel in your work environment. If you’re working on a vehicle fuel system, you need a product that’s been tested rigorously and will hold up in a shop setting. Otherwise, you’re dealing with a major fire hazard.
A U.L. listed fuel caddy’s features include flame arresters on the openings, grounding cables, non-sparking foot plates, and fill gauges. This type of fuel caddy will pass Occupational Safety and Health Administration (OSHA) and fire marshal inspections.
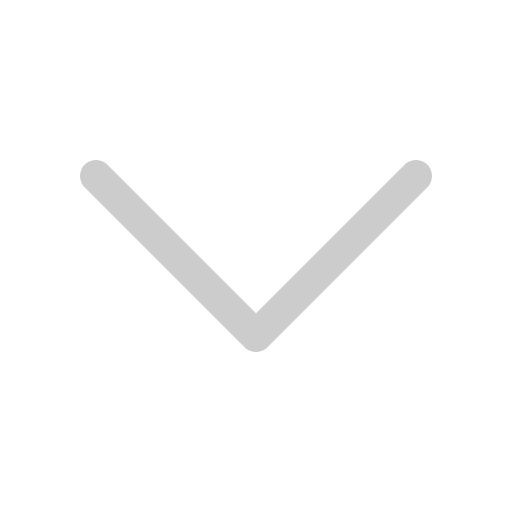
Do I need a UN/DOT approved fuel caddy?
You should use a UN/DOT-approved poly fuel caddy when you’re going to transport fuel on public roads. The label means the fuel caddy was approved by the United Nations (UN) and the U.S. Department of Transportation (DOT). This packaging is a universal means of ensuring safe transport of dangerous materials.
When you’re transporting more than five gallons of fuel, most municipalities require a UN/DOT-approved container. If you don’t have the right gas caddy, you could find yourself in trouble with local law enforcement. You also get peace of mind that your container can safely transfer fuel.
EXPLORE MORE
Over-Tightening drain plug can lead to oil leaks for 2024 Nissan Rogue and Murano
Smaller, inexpensive parts can take up time in your bays. Don't hold up a sale by not having the right part at the right time!
Learn MoreUnderstanding the Lockout/Tagout Process
If you repair or plan on repairing EV or Hybrids in your shop, you need to understand what you'll need to do before performing any repair service.
Learn MoreWhat to look for when shopping for a vehicle fire blanket
When buying a vehicle fire blanket, keep in mind price, flexibility, usage, material, and temperature rating.
Learn MorePrecision in Every Drop: JohnDow's Superior Fluid Handling Equipment
Top-tier vehicle fluid handling solutions in the automotive equipment industry, from gas and oil handling to adapting for electric vehicles (EVs).
Learn More